(Review article)
Recent progress on metallic glasses in Taiwan
J. C. Huang*, J. P. Chu, J. S. C. Jang
1 Department of Materials and Optoelectronic Science; Center for Nanoscience and Nanotechnology, National Sun
Yat-Sen University, Kaohsiung, Taiwan 80424, ROC
2 Department of Polymer Engineering, National Taiwan University of Science and Technology, Taipei, Taiwan 10607,
ROC
3 Department of Materials Science and Engineering, I-Shou University, Kaohsiung, Taiwan 84001, ROC
*Corresponding author. Tel: +886 7 5252000 ext. 4063; fax: +886-7-5254099.
E-mail address: jacobc@mail.nsysu.edu.tw (J.C. Huang)
Abstract The recent research and development on metallic glasses in Taiwan over the past decade is reviewed in this
paper. The major focus was to develop tougher bulk metallic glasses (BMGs), bulk metallic glass composites (BMGCs),
and thin film metallic glasses (THMGs), mostly in Zr and Mg based systems. Due to the Taiwan industry characteristics,
metallic glasses are favored in the application for micro-electro-mechanical systems (MEMS), including micro- or
nano-imprinting for optoelectronic devices and hologram patterns.
Keywords: B. glasses, metallic; B. mechanical properties at ambient temperature; C. rapid solidification processing; B.
thermodynamic and thermochemical properties
|
1. Introduction
Metallic glasses have been one of the extensive research subjects over the past twenty years. The unique
properties such as high strength and hardness, special
damping property, soft magnetic characteristics, and
oxidation/corrosion resistance enable this new category
of metallic materials to be applied for structural or
functional applications. Before 1990’s the research and
development (R&D) focuses of metallic glasses were
mainly on the Au-Si and Pd based system. After the
breakthrough in early 1990’s, many other systems such
as La, Mg, and Zr based bulk metallic glasses (BMGs)
were developed. So far, the existing and on-going efforts
have developed numerous successful systems, including
Zr, Fe, Mg, Au, Pd, Pt, Cu, Ni, Ti, Co, Al, Ce, Ca, La,
and many other rare-earth based amorphous alloys, as
reviewed in a number of review papers [1-5].
In addition to the metallic glasses in the bulk form,
recently, metallic glasses have been extended to the thin
or thick film area, in an attempt to find applications in
the micro-electro-mechanical systems (MEMS). For such
applications, the amorphous alloys sometimes need to be
fabricated via the sputtering or other thin film processes.
The as-deposited thin film metallic glasses (TFMGs)
usually exhibit a uniform composition without
micro-segregation, avoiding the possible local
crystallization during the fabrication process.
The initial R&D activities of the BMGs and
THMGs in Taiwan start from early 1990’s, in academic
university such as National Tsing-Hua University and
National Taiwan Ocean University, as well as in research
institutes such as Industry Technology Research Institute
(ITRI) and Chung-Shan (Military) Institute of Science
and Technology. The initial R&D was aimed on the Zr,
Mg and Fe based BMGs. Later research was
continuously extended in several universities, such as
National Sun Yat-Sen University, I-Shou University and |
National Taiwan Ocean University, together with the
reinforcement from Metal Industries Research &
Development Centre (MIRDC). The major joint efforts
were lunched in 2000’s. An international collaboration
project on metallic glasses was approved in 2005,
covering eight research laboratories in National Sun
Yat-Sen University, National Taiwan Ocean University,
I-Shou University, National Cheng-Kung University and
National Taiwan University of Science and Technology,
as well four USA laboratories in Oak Ridge National
Laboratory, University of Tennessee, and University of
Wisconsin, Madison. MIRDC was also involved to
promote industry applications.
2. Alloy design
The initial alloy design was limited to the Zr based
BMGs [6-13]. Effects of individual micro-alloying with
Si (0~10 at%) or B (0~4 at%) on the thermal properties
of the Zr65Cu17.5Ni10Al7.5 base alloy have been
systematically investigated. It is found that the addition
of either B or Si would posses a positive effect on
thermal stability improvement of the base alloy, while
keeping the same glass forming ability (GFA) as the base
alloy. The largest activation energy of crystallization,
about 360 kJ/mol, occurs at the compositions of
Zr63Cu17.5Ni10Al7.5B2 and Zr61Cu17.5Ni10Al7.5Si4.
Furthermore, the Zr65-x-yAl7.5 Cu17.5Ni10SixBy alloy system,
where x = 0~4 and y = 0~2, was selected for studying the
effect of simultaneously adding B (with a smallest
atomic size) and Si (with a negative heat of mixing) on
its crystallization and thermal stability. The experimental
evidence and the kinetic analyses revealed that, with the
addition of 4 at% Si and 1 at% B, the Trg (=Tg/Tl) and
γ (=Tx/(Tg+Tl), where Tg, Tx, and Tl are the glass
transition, crystallization, and liquidus temperature,
respectively) values increase from 0.57 and 0.40 for the
Zr65Al7.5Cu17.5Ni10 base alloy to 0.62 and 0.43, |
suggesting the improved glass forming ability. The
saturation point for nucleation for 4%Si-1%B and
1%Si-2%B amorphous alloys occurs at the 88%
crystallization fraction, much higher than the 65% for the
base alloy [10-12], implying that these metalloid
elements would extend the nucleation stage and result in
smaller crystalline particles. Moreover, the variation of
the incubation time, as shown in Fig. 1 [6], exhibits an
increasing trend with increasing silicon addition, directly
supporting that the Si addition would improve the
thermal stability of the Zr65Al7.5Cu17.5Ni10 base alloy.
Parallel studies have also been done on the
Zr53Cu30Ni9Al8 amorphous alloy [13] which
computationally designed by thermodynamics and deep
eutectic methodology [14]. The improvement of thermal
stability by the Si addition is contributed by the increase
of their atomic packing density as well as their Zr-Si and
Ni-Si strong atomic bonding, promoting the coating of Si
thin layer on the nanocrystalline Zr2Ni phase [6].
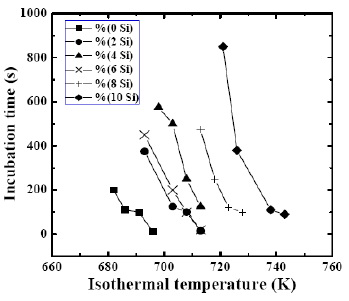
Fig. 1 Incubation time as a function of isothermal
temperature for the Zr65-xAl7.5Cu17.5Ni10Six alloys with Si
content from 0 to 10at% [6].
The Mg65Cu25-xGd10Agx alloy system was
systematically investigated to reveal the effect of Ag (in
substituting Cu) on the GFA and crystallization behavior
of the base alloy [15]. Because of a large difference in
atomic size between Ag and the constituting elements;
the atomic radius of Ag is larger than that of Cu by 11%
and is smaller than those of Mg and Gd by 10% and
19.5%, respectively, the atomic packing density of the
Mg65Cu25-xGd10Agx alloy would increase with increasing
Ag content and concurrently increase its GFA. The
highest γ value (0.407) and a relatively high Trg (0.58)
occur at the Mg65Cu22.5Gd10Ag2.5 alloy. More recently,
new optimum alloy designs are made based on the recent
model of optimum composition extension from the
binary eutectic pairs, originally proposed by Lu et al.
[14]. This model suggests that the optimum Mg based
BMGs might possess a composition with a lower amount
of Mg and a higher amount of rare earth (RE) element,
for example, the Mg58Cu31Y11 and Mg58Cu31Gd11[16,17].
A series of Mg based BMGs with 50-60at% Mg and
10-15at% dual RE elements (Nd and Y) are prepared by
atmosphere controlled induction melting and injection
casting methods [18]. The selection of Nd for partially
replacing Y element is inspired by the facts such as the
difference between Nd and Y in covalent atomic radius
(Nd: 0.164 nm; Y: 0.162 nm), electronegativity (Nd: 1.14,
Y: 1.22), electronic configuration (Nd: 4f45d06s2, Y:
4d15s2), and near-zero heat of mixing of the Y–Nd binary
|
system (forming continuous solid solutions). These
differences may result in certain change of short range
ordering in the undercooled liquid of the
Mg58Cu31Y11-xNdx alloys, favoring the glass formation.
The recent results revealed that the highest γ value (0.414)
and a relatively high Trg (0.55) occur in the
Mg58Cu31Y6Nd5 and Mg58Cu31Y4Nd7 alloys. In addition,
a BMG rod with 10 mm in diameter can be produced for
Mg58Cu31Y6Nd5 alloy by a Cu mold injection casting.
The effects of adding small sized B to replace Cu or
Y in the Mg65Cu25Y10 based alloy have been examined
[19]. It is found that the replacement of Y by B
consistently leads to apparent degradation in GFA; the
only large-sized Y seems to be irreplaceable. In contrast,
the replacement of the small-sized Cu by the even
smaller B to a small amount (1-5%) appears to be
beneficial in terms of wider ΔT, higher GFA and
hardness. The optimum quaternary alloy composition is
located to be Mg65Cu22Y10B3. It is also found that the
thermal stability and crystallization energy can be
enhanced by the small addition of B [20].
Using the computational-thermodynamic approach,
the potential compositions of Zr-Cu-Ni-Al alloy system,
exhibiting the two-liquid miscibility phase equilibrium in
the liquid temperature region, have been identified [21].
It was noted that the Zr–Cu–Ni–Al alloy system is a
good candidate for this investigation, since it shows a
high GFA and includes an atomic pair with a positive
enthalpy of mixing between Ni and Cu elements (+4
kJ/mol). Since the positive heat of mixing between Cu
and Ni is very slight, how to pinpoint the composition of
an alloy exhibiting phase separation appears to be a
scientific challenge. The Zr based bulk metallic glasses
with the composition predicted by the thermodynamic
calculations, Zr63.8Ni16.2Cu15Al5 for the 5% Al alloy
series, show a microstructure of two micro-scaled glassy
phases, as shown in Fig. 2 [21]. According to the
solution thermodynamic principle, there are positive
mixing-enthalpy values to induce the two-liquid
miscibility region. The spinodal lines can be calculated
based on the conditions that the second derivate of
Gibb’s free energy is equal to zero within the two-liquid
miscibility region. In parallel studies using
thermodynamic computations [22,23], such spinodal
boundaries can be carefully established. The liquid
composition within the spinodal region may decompose
into two liquid phases assigned as Ni-rich liquid and
Cu-rich liquid and form the two-liquid metallic glass.
The designed alloy composition is selected, namely,
Zr65.8Ni15.8Cu8.4Al10 for the 10% Al series. Both
Zr63.8Ni16.2Cu15Al5 and Zr65.8Ni15.8Cu8.4Al10 lie within the
spinodal region. It should be noted that the predicted
alloys all have more Ni than Cu, different from most
Zr-based BMGs containing more Cu than Ni, as the
typical one reported by Zhang et al. [24].
During the alloy design for optimum BMGs, the
GFA index was also part of the study. There have been a
number of indices to evaluate the glass forming ability of
BMGs, such as γ (=Tg/Tx+Tl), Tx/Tl, ΔTx (=Tx-Tg), Trg
(=Tg/Tl), Tx/(Tl-Tg), Tg/Tl+Tx/Tg and (Tx-Tg)/(Tl-Tg),
where Tg is the glass transition temperature, Tx the
crystallization temperature, and Tl the liquidus |
temperature. In 2007, it was further developed some
more reliable parameters, one is γm=(2Tx-Tg)/Tl [25,26],
and the other is κ=ΔTx/Tx+ Tg/Tl [27]. The existing
experimental data can be fit into the trend to confirm that
the γm and κ parameters exhibit the best correlation with
GFA among all parameters suggested so far for bulk
metallic glasses, due to the fact that the new indicator
considers all related factors for the liquid phase stability
during cooling and the resistance to crystallization during
heating.
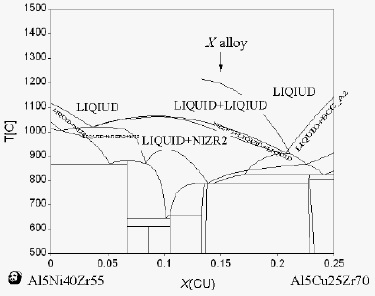
Fig. 2 The simulated phase diagram for the
composition cut between Al5Ni40Zr55 and Al5Cu25Zr70
[21].
Fe based soft magnetic BMGs have been studied
by Chin and his coworkers in National Tsing Hua
University [28-30]. A new simple ternary Fe76B20Y4
BMG rod measuring 2 mm in diameter was developed
with a high saturation magnetization of 1.56 T, low
coercivity less than 40 A/m, and high electrical
resistivity larger than 200 mV.cm [28]. Other Fe based
amorphous and nanocrystalline melt-spun ribbons with
promising soft magnetic properties are continuously
explored [29].
In addition, the new ternary Ni-Ta-Sn ternary BMG
system was also developed, with 33<Ta<38 and 2<Sn<9
(in at%). The alloy shows a wide BMG forming regime.
The crystallization temperature is among the highest in
Ni based BMGs, with a wide supercooled liquid region
57–61 K. This Ni-Ta-Sn BMG shows high hardness,
typically Hv~1000, and a compressive fracture strength
856–1192 MPa. The Ni58Ta36Sn6 BMG also exhibit good
corrosion resistance in the anodic region [30].
The synthesis and characteristics of the Mg based
BMG composites (BMGCs) have been studied in I-Shou
University [31-35]. The Mg based BMGCs are fabricated
through mechanical alloying (MA) in the planetary mill,
using amorphous Mg65Cu25-XY10Agx (x=0, 5, 10) matrix
alloy prepared by melt spinning and 1-5 vol% spherical
nano-sized ZrO2 particles. The melt spun amorphous
matrix ribbons are ground into powders and mixed with
the ZrO2 nano particles in the planetary mill, followed by
hot pressing in Ar atmosphere under different pressures
at the temperature 5 K above the glass transition
temperature. Throughout the MA and hot pressing
processes, the Mg based BMGCs exhibit an amorphous
Mg65Cu20Y10Ag5 matrix microstructure with 80-nm nano
ZrO2 particles homogeneously dispersed. The
microstructure near the interface between the matrix and
nano particles presents a well bonded condition. In
addition, the hot-pressed composite can reach a 96% |
density, 360 in Hv hardness, and 700 MPa for the
compressive strength. Moreover, the toughness of the
Mg based BMGCs exhibit an increasing trend with
increasing nano-sized ZrO2 content, and can reach a level
of 8.9 MPa.m0.5 [32,33].
3. Fabrication
The fabricating routes for the BMGs in I-Shou
University and National Sun Yat-Sen University are
either injection or suction casting, with arc or induction
furnace. For producing the Zr based (or CuZr based)
BMGs, an atmosphere-controlled
arc-melting/suction-casting process is the preferable way
to prepare the Zr based alloys. The rods with dimension
of 8 mm φ x 70 mm L and plates with dimension of 3
mm T x 30 mm W x 60 mm L of the Zr based BMGs can
be successfully fabricated by this method. On the other
hand, for making the Mg based BMGs and BMGCs,
two-steps atmosphere control induction melting and
injection-casting process is in use to prepare the highly
reactive and high vapor-pressured Mg based alloys. The
rods with dimension of 10 mm φ x 60 mm L and plate
with dimension of 2 mm T x 20 mm W x 60 mm L of the
Mg based BMGs can be successfully prepared. Some
examples are shown in Fig. 3.
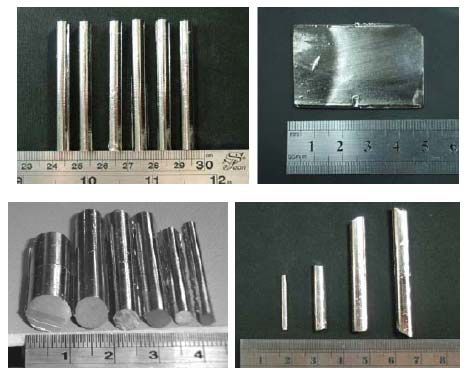
Fig. 3 Showing the Zr- or Mg-based based BMG rods
and plates in various dimensions.
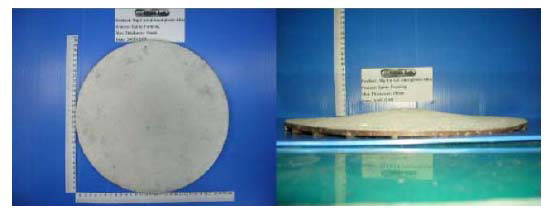
Fig. 4 Morphology of a spray-formed Mg–Cu–Gd
layered composite plate with a Gaussian-shape, and 300
mm in diameter, 12 mm in maximum thickness, and 510
g in mass [40].
Spray forming has also been applied to fabricate Al
and Mg based amorphous plates measuring 1 to 10 mm
in thickness in National Cheng Kung University [36-40].
Spray forming can be considered as an intermediate
processing between casting and deposition, with a
cooling rate in the range of 1-100 K/s. Spray forming
was firstly employed to fabricate Al89La6Ni5 based
BMGs and later Mg-Cu-Y or Mg-Cu-Gd systems, as |
shown in Fig. 4 [40].
BMGs and BMGCs have been fabricated using the
mechanical alloying and consolidation methods [41-48].
Examples include the Mg and Ti based amorphous
composites with additives of WC, SiC, carbon nanotube
(CNT) powders. It is found that mechanical alloying may
cause partial dissolutions of the additives, and thus the
thermal stability of the amorphous matrix is altered due
to the deviation in chemical composition of the glassy
matrix. Yet, the supercooled liquid region of resulting
materials remains almost unchanged. Compared with the
pure amorphous structure, the hardness of the BMGCs
increases as much as 30% due to the presence of
additives. The composites suffer partial crystallization
during the consolidation process in the supercooled
liquid region.
The amorphous materials have also been prepared
by accumulative roll bonding (ARB) via room
temperature cold rolling in the solid state for alternating
thin layers of various metals with a special arrangement
of composition [49-56]. Binary Zr-Ti, Zr-Ni, Zr-Cu and
Zr-Al, ternary Zr-Cu-Ni, quaternary Zr-Cu-Ni-Ti and
pentanary Zr-Cu-Ni-Ti-Al systems were systematically
explored. It is found the crystalline foils can be mixed
into homogeneous nanocrystalline and/or amorphous
phase with increasing ARB cycles. After around 80 to
120 cycles, the alloys can be mostly transformed into the
amorphous matrix, as shown in Fig. 5 [49]. Note that the
volume fractions of the remianed nanocrystalline phases
and the interdiffusion-induced amorphous matrix can be
controlled by the applied ARB cycle, as depicted in Fig.
6 [51]. For example, if an alloy is designed to possess
around 50% amorphous phase in Zr-Cu system, then
about 80 ARB cycles are needed. At that time, the
remaining nanocrystalline pure Zr or pure Cu phases are
about 20 nm in size. The diffraction spots and rings in
the TEM diffraction patterns of the ARB specimens are
all originated from the pure elements, meaning that the
nanocrystalline phases are those unmixed hard particles
left from the previous severe deformation and diffusion
processes. A critical size of the nanocrystalline phases
around 3 nm is consistently observed in all binary,
ternary, and pentanary Zr-X based alloys, below the
critical size a sudden transformation from the
nanocrystalline to amorphous state would occur [50-54],
as shown in Fig. 7 [50].
The friction stir process with effective liquid
nitrogen cooling has also been adopted in preparing the
MgAlZn intermetallic compound alloys, with
nanocrystalline icosahedral particles plus a certain
amount of amorphous phases [57,58].
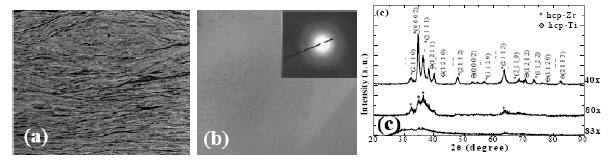
Fig. 5 (a) The stacked Zr and Ti foils after 50 ARB
cycles, (b) typical TEM micrograph and electron
diffraction pattern of the vitrified Zr50Ti50 region by ARB,
and (c) typical XRD patterns of the ARB Zr50Ti50
samples after different cycles at room temperature [49]. |
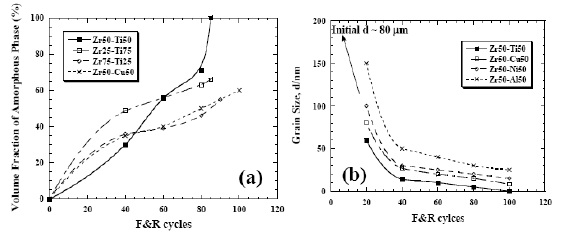
Fig. 6 The variations of (a) nanocrystalline grain size
and (b) amorphous volume fraction in various Zr–X
alloys as a function of ARB cycles, based on the X-ray
diffraction results [51].
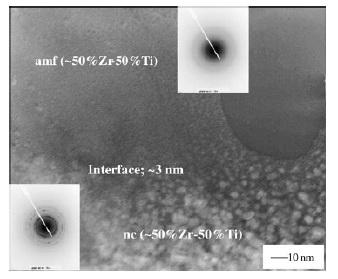
Fig. 7 TEM bright field images of the interface region
between the nanocrystalline and amorphous phases. The
smallest nc phase size near the interface is around 3 nm
[50].
4. Mechanical behavior
Extensive research has been devoted to the
mechanical properties of BMGs, in an attempt to develop
strong and tougher BMGs, as described below in Sec. 5.
The effect of the compression specimen aspect ratio was
examined in the Mg based BMGs [59].
Room-temperature compression tests are conducted on
specimens with various height-to-diameter ratios (h/d)
from 2:1, 1:1, 1:2, to 1:4. The failure strength,
deformation strain, and the fracture surface morphologies
are seen to vary systematically in accordance with the
specimen h/d ratio. For specimens with h/d of 2:1 or 1:1,
the compression response is similar to those in most
reports. In contrast, for specimens with lower h/d ratios,
especially at h/d = 1:4 (or 0.25), the shear band
propagation appears to be constrained by the top and
bottom platens, resulting in the enhanced ductility.
Micro-pillars with a diameter of 1 and 3.8 μm were
fabricated from the Mg based metallic glasses using
focus ion beam, and then tested in micro-compression at
strain rates ranging from 6x10-5 to 6x10-1 s-1, as shown in
Fig. 8 [60]. The strength of the micropillars varies within
1342-1580 MPa, or 60-100% increment over that of the
bulk specimens. This strength increase can be
rationalized using the Weibull statistics for brittle
materials, and the Weibull modulus (m) of the Mg based
metallic glasses is estimated to be about 35. The surface
examination of the micro-pillar specimens indicates that
the number of shear bands increase with the sample size
and strain rates.
The specimen size dependence was also explored
in the more ductile Zr based metallic glasses (with
phase-separation [21]), covering rod specimens with
diameters of 2-4 mm down to micro-pillars with
|
diameters of 0.7 to 4 μm [61]. The increment of strength
is also analyzed in terms of the Weibull statistics. The
extracted Weibull modulus is ~60 for this ductile
phase-separated Zr BMGs [61], compared with the
values ~35 and ~40 for the brittle Mg based BMGs [60]
and Au49Ag5.5Pd2.3Cu26.9Si16.3 BMG [62]. These results
are consistent with other reported Weibull modulus
values for the malleable Zr48Cu45Al7 (m=73.4) [63] and
brittle (Zr48Cu45Al7)98Y2 (m=25.5) [63]. It seems that the
size dependence is related to the ductility and cast defect
of the amorphous alloys.
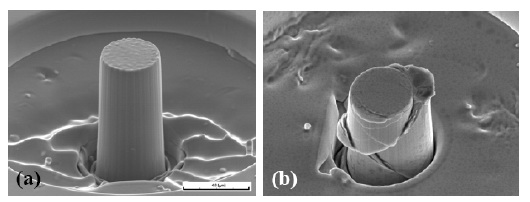
Fig. 8 Micro-pillars prepared by focus ion beam: (a)
before micro-compression and (b) after
micro-compression to about 30% strain [60].
5. Toughening
The current critical issue for metallic glasses appears
to be the toughening of their brittle nature. Based on
previous efforts, the most promising approaches might
be the enhancement of the Poisson ratio by tailoring the
compositions, the employment of in-situ phase
separation to form an amorphous matrix mixed with a
dendrite crystalline phase (forming a dendrite-reinforced
amorphous composite) or a second glassy phase (forming
a dual-phased glass) [21-23]. Tremendous efforts have
been made in terms of the above approaches. One is to
form liquid phase separation at high temperatures during
induction melting, followed by rapid quenching to form
the phase-separated glass. Successful results in Zr based
glasses (e.g., Zr63.8Ni16.2Cu15Al5 or Zr65.8Ni15.8Cu8.4Al10)
have achieved compressive ductility over 30%, as shown
in Fig. 9 [21]. Another approach is to employ the porous
particles into the amorphous matrix to form an
amorphous matrix composite. Successful results in Mg
based glasses added with 5-25 volume percent of porous
Mo particles (~30-50 μm) have achieved compressive
ductility over 10%, as shown in Fig. 10 [64]. Both these
two approaches are designed with the concept in
separating the homogeneous glassy matrix into numerous
individual compartments with smooth but distinctive
interfaces. The complicated interaction of propagating
shear bands with these compartments and interfaces
would promote multiple shear banding and resulting in
improved ductility.
The gain of high compressive strength and
remarkable macroscopic plastic strain of 30% in the
phase-separated Zr63.8Ni16.2Cu15Al5 or
Zr65.8Ni15.8Cu8.4Al10 is attributed to the unique glassy
structure correlated with the chemical inhomogeneity on
the micron scale; the hard phases surrounded by the soft
phases, leading to an inherent capability of extensive
shear-band formation, interactions, and multiplication
[21-23]. The work shows that, by the two-liquid phase
separation in accordance with the thermodynamic |
prediction, a good-GFA and ductile BMG can be
achieved from the two-glassy-phase microstructure.
Recent works on the Mg based BMGs added with
micro-scaled Fe [65] or Ta [66] particles are under
investigation. The BMGCs of these systems also show
compression plasticity over 10%. The brittle nature of
the Mg based BMGs can be sufficiently toughened by
the Fe and Ta particles.
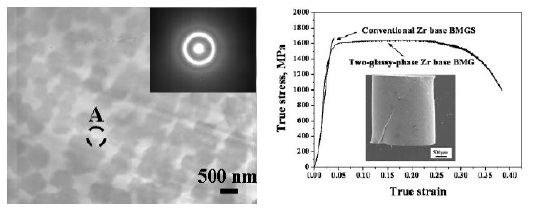
Fig. 9 (a) TEM bright-field image, with an inserted
electron diffraction pattern, of the 2 mm Zr-based BMG
rod with micro-scaled phase separation, (b)
room-temperature stress-strain curve for as-cast 2 mm
diameter cylinders. The inset shows the deformed sample
[21].
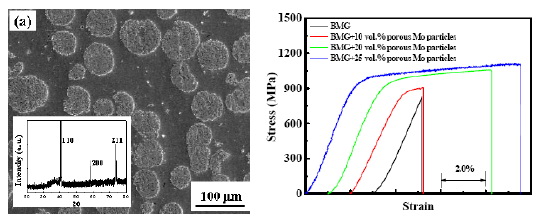
Fig. 10 (a) SEM micrograph of the homogeneous
distribution of porous Mo particles in the Mg-based bulk
metallic glasses, with the inserted X-ray diffraction
pattern, (b) representative room-temperature compressive
engineering stress-strain curves for the as-cast 2 mm
diameter compression specimens. The curves are shifted
relative to each other for clarity [64].
6. Modeling
Molecular dynamics (MD) simulation was applied
for the structural evolution and mechanical response of
the metallic glasses using the tight-binding potentials for
the elements [53-56]. For the simulation for the ARB
solid-state vitrification process, the molecular dynamics
simulation reveals that it needs only 6 cycles for a
bi-layer structure, with 5 nm in each layer thickness, to
fully transform into a completely amorphous state, as
shown in Fig. 11 [54]. The potential energy between two
distinct atoms increases during the transition between
nanocrystalline and amorphous state due to the severe
structure change. It increases the difficulty for atoms to
maintain the crystalline structures. The values of the
nearest neighboring distance extracted from the
transmission electron microscopy (TEM) observation
and the MD simulation are both smaller than the
theoretically calculated value. A new tighter packing
atomic structure in the Zr50Ni50 amorphous alloy is
formed due to the large negative mixing enthalpy.
The gradual vitrification evolution of atom mixing
and local atomic pairing structure of the binary Zr-Ni
alloy during severe deformation at room temperature is
|
traced numerically by MD simulation in terms of the HA
index (Fig. 12 [67,55]) developed by Honeycutt and
Anderson [67]. It is found that the icosahedra clusters
will gradually develop with increasing disorder
environment of alloys. Other compound-like transition
structures were also observed as transient in the Zr-Ni
ARB couple during the solid-state amorphization process
under severe plastic deformation. Since the time scale of
the MD simulation is several orders of magnitude shorter
than reality, the simulated atomic evolution can be
viewed as that would occur at ultra-high strain rates.
Simulation of the deformation behavior and shear band
evolution during indentation, compression and fatigue
loading is now undertaken.
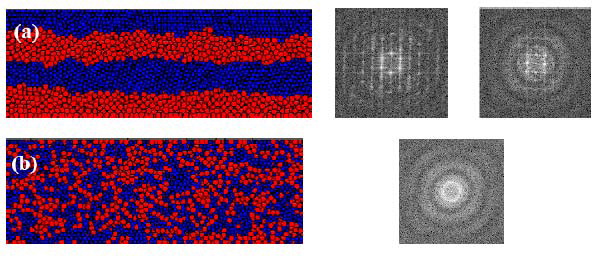
Fig. 11 The microstructural evolution and the associated
two-dimensional Fourier transform of the bi-layered
Zr50Ni50 model subjected to various ARB cycles: (a)
initial state with the distinct Fourier transformed
diffraction patterns for crystalline Zr and Ni, and (b)
after 6 ARB cycles with the Fourier transformed
diffraction patterns for an amorphous structure [54].
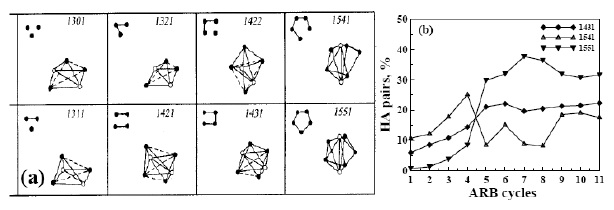
Fig. 12 (a) The schematic drawing of the related HA
pairs [67]. (b) Variations of the HA indices of the Zr-Ni
alloys during different ARB cycles: 1431, 1541, and
1551 [55].
7. Thin film metallic glasses
The vapor-solid quenching during sputtering
enables the amorphous or nanocrystalline phases to form.
The thin film amorphous alloys are generally called as
the thin film metallic glasses (TFMGs), which can be
prepared by many physical vapor deposition methods
such as sputtering or evaporation. TFMGs might have
tremendous application potentials in the areas of surface
coating and MEMS [68,69]. Co-sputtering by two or
three guns appears to be a promising process in studying
the TFMGs with a wide variation of composition and
microstructure.
It is also the first to report annealing-induced
amorphization in glass-forming Zr47Cu31Al13Ni9 [68] and
Fe65Ti13Co8Ni7B6Nb1 [69] films at a temperature within
the supercooled liquid region (Fig. 13 [69]). The
extensive amorphization is presumably attributed to
sufficient thermal and interfacial energies between
nanocrystallites and glassy matrix that are present in the |
as-deposited condition. The formation of comprehensive
amorphous structure gives rise to notable alterations in
the electrical, mechanical and magnetic properties of
annealed films (Fig. 14 [68]). Important feature of these
works is that a prominent strengthening effect is
observed due to the amorphous matrix dispersed with
nanocrystalline phases upon annealing. In addition, the
glass-forming film coating is applied to improve the
fatigue properties of material for the first time [70,71].
The excellent adherence and the smooth film surface
have a noticeable influence on the fatigue life. With the
deposition of the Zr47Cu31Al13Ni9 glass-forming film, the
fatigue life of the 316L stainless steel could be increased
by 30 times, and the fatigue limit could be elevated by
30%, depending on the maximum stress applied to the
steel (Fig. 15 [70]). The high strength and the good
bending ductility might be other important factors for the
improvement.
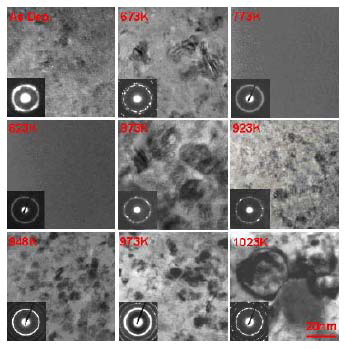
Fig. 13 Typical TEM bright-field images and
diffraction patterns of the Fe65Ti13Co8Ni7B6Nb1 films in
as-deposited and annealed conditions [69].
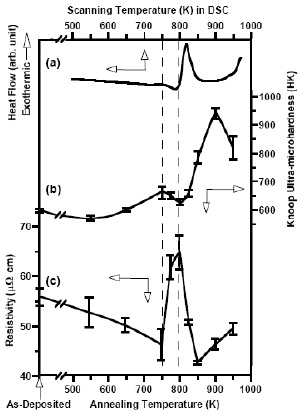
Fig. 14 (a) DSC thermogram of an as-deposited
Zr47Cu31Al13Ni9 film; variations of (b) Knoop
ultra-microhardness and (c) electrical resitivity with the
annealing temperature. Approximate location of
supercooled liquid region is marked by the dash lines to
facilitate visual comparison [68]. |
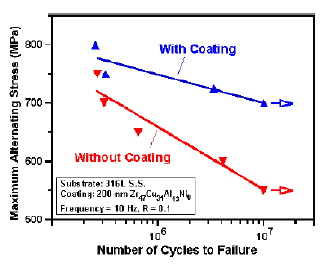
Fig. 15 Stress versus fatigue cycle for samples with and
without the Zr47Cu31Al13Ni9 film. Arrows indicate the
run-out data without the failure [70].
In addition, the fully amorphous thin films can be
easily prepared by co-sputtering of the Zr-Cu or Zr-Cu-Ti
systems [72,73]. Partial amorphous thin films can be
achieved by co-sputtering of Mg-Cu system [74], or
multilayer sputtering plus post-annealing in the Zr-Cu
system [72].
8. Oxidation and corrosion
The high-temperature oxidation behaviors of the Zr
and Cu based BMGs in dry air or oxygen environment
have been systematically examined by Kai and his group
[76-82], including Zr53Ni23.5Al23.5 at 400-600°C [76],
Cu60Hf25Ti15 at 375-520°C [77], Cu60Zr30Ti10 and
Cu60Zr20Ti10Hf10 at 350-500°C [78], (Cu78Y22)98Al2
amorphous composite at 400-600°C [79] and other
systems [80-82]. For the Zr53Ni23.5Al23.5 system at
400-600°C [76], the oxidation kinetics of the alloy
follow the single- or two-stage parabolic rate law at T ?
500°C, but could be fitted by a three-stage parabolic law
at 550-600°C. They found the amounts of Al2O3 and
monoclinic-ZrO2 in the scales increase with the oxidation
temperature. Based on the crystallographic and
microstructural characterization results, they suggest
more complicated oxidation kinetics at the temperature
near Tg (such as 500°C) and above; this might have
resulted from the fact that crystallization of oxidation
take place simultaneously.
For the Cu60Hf25Ti15 system at 375-520°C [77],
they found that the oxidation rates of the amorphous
alloy are much higher than those of polycrystalline pure
Cu, and suggested that the additions of Hf and Ti
accelerate the oxidation reaction. To determine the
oxidation mechanism of the alloy, marker studies
performed at 425°C for 72 hours show Pt markers were
always located on the scale surface, indicating that the
oxidation mechanism is involved mainly inward
diffusion of oxygen. In addition, they detected Cu51Hf14
and Cu3Ti2 phases in X-ray diffraction (XRD) results,
indicating the occurrence of phase transformation during
the oxidation test. In comparing the Cu60Zr30Ti10 and
Cu60Zr20Ti10Hf10 systems at 350-500°C [78], they found
the addition of Hf slightly reduce the oxidation rate of
alloy at 350-400°C while the reverse situation is
observed at higher temperatures. The scales formed on
both alloys were strongly composition dependent,
consisting of mostly CuO/Cu2O and minor cubic-ZrO2
and ZrTiO4 for the ternary BMG, and of CuO,
|
cubic-ZrO2, and Zr5Ti7O24 for the quaternary BMG.
They concluded that the formation of ZrTiO4 and
Zr5Ti7O24 is responsible for the faster oxidation rates of
these BMG alloys.
In addition, the oxidation of the (Cu78Y22)98Al2
amorphous composite containing Cu5Y at 400-600°C
was also examined [79]. It is found that the
Cu5Y-bearing composite has lower oxidation rates than
those of the (Cu78Y22)98Al2 amorphous and pure Cu. The
XRD and scanning electron microscopy (SEM)
characterizations on scales formed during oxidation
reveal that the scales formed on the Cu5Y-bearing
composite consist of mainly hexagonal-Y2O3 and minor
CuO. On the other hand, the scales on (Cu78Y22)98Al2
amorphous alloy are largely Cu2O and CuO with minor
amounts of Y2O3. Accordingly, they concluded that the
presence of Cu2O is responsible for the poor oxidation
properties of (Cu78Y22)98Al2 amorphous alloy.
In addition to oxidation, the corrosion properties of
the Pd, Fe and Cu based BMGs were also studied in
Taiwan [83-86]. They evaluated the corrosion properties
of these alloys in various aqueous solutions such as NaCl,
HNO3, H2SO4, and HCl. They found that the alloys in
amorphous state normally have better corrosion
properties than those of crystalline state. For example,
after crystallization by vacuum annealing at 650°C for 1
hour, the corrosion resistance of the F40Ni38B18Mo4 alloy
under its crystalline state becomes inferior to its
amorphous state [83]. But for some other cases, they also
reported that the corrosion resistance of amorphous alloy
can be improved about two to three times by annealing.
This is particularly found in the Pd40Ni40P20 alloy [84].
Their XRD result of the annealed sample shows the
presence of several phosphides and palladium which
behave as inert phases mixed with noble metal to
enhance corrosion resistance.
The corrosion behavior of the Ni58Ta36Sn6 1-mm
BMG rods was measured in HCl aqueous solution, open
to air at 25oC. The polarization curve of pure tantalum is
also displayed to contrast with the Ni–Ta–Sn BMG. In
anodic region, the alloy spontaneously passivates. After a
potential larger than 0.3 V, a passivation current density
is noted as being slightly lower than that of pure
tantalum. The open-circuit potential of the glassy alloy is
about 0.13 V, being nobler than that of pure tantalum
[75].
In addition, they studied hydrogen permeation of
amorphous Fe based alloys, focusing on alloying element
effects [85]. They pointed out that the apparent solubility
of hydrogen in Fe81B13.5Si3.5C2 is higher than that in
Fe40Ni38B18Mo4 because of the hydrogen-trapping effect
of carbon and silicon atoms. They further reported that
the presence of smaller atoms of carbon and silicon
results in decreases in hydrogen permeation rate and
effective diffusivity in the Fe81B13.5Si3.5C2 alloy.
Moreover, they evaluated the corrosion behavior of
mechanically alloyed Cu60Zr30Ti10 BMG in different
corrosive solutions using the potentiodynamic method
[85]. The glassy alloy exhibits the most corrosion
resistance in H2SO4 solution, while, in NaCl solution,
there is the pit growth on the surface leading to
breakdown of the passive film due to the galvanic |
corrosion mechanism [85].
9. Thermomechanical behavior
The viscous flow behavior of the Mg58Cu31Y11
bulk amorphous rod in the supercooled viscous region is
investigated using differential scanning calorimetry
(DSC) and thermomechanical analyzer (TMA) [87].
Below the glass transition temperature, Tg, a linear
thermal expansion coefficient of 3±1x10-6 m/m.K was
obtained. In contrast, significant viscous deformation
occurred as a result of a compressive load above Tg. The
onset, semi-steady-state, and finish temperatures for
viscous flow, determined by TMA, are slightly different
from the glass transition and crystallization temperatures
measured by DSC. All these characteristic temperatures
decrease with increasing applied stress, suggesting
accelerated crystallization in the present Mg58Cu31Y11
under stress. The appropriate working temperature for
microforming as determined by the semi-steady-state
viscous flow temperature is about 460-474 K. The
effective viscosity within this temperature range is
estimated to be about 107-109 Pa.s, and it increases with
increasing applied stress, as demonstrated in Fig. 16(a)
[87]. The viscosity behavior of the Mg based BMGs falls
in-between the strong SiO2 glass and the polymer
o-terphenyl fragile glass, as shown in Fig. 16(b) [87].
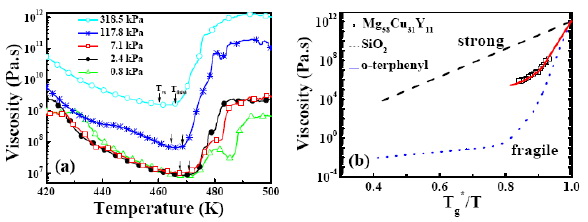
Fig. 16 (a) Temperature dependence of the effective
viscosity for the indicated applied stress at a heating rate
of 10 K/min.(b) The viscosity data on Mg58Cu31Y11 (or
the Angell plot). The data on the strong SiO2 and fragile
o-terphenyl glasses are compared with Mg58Cu31Y11 [87].
The viscous flow behavior and thermomechanical
properties of Mg65Cu25-xBxGd10 (x = 0 and 3 at%) [88]
and Mg65Cu25-xAgxGd10 (x=0, 3, 10 at%) [89] BMGs in
the supercooled liquid region have also been investigated.
It is found that the fragility of the supercooled liquid is
reduced by the boron or silver addition, thus degrading
the deformability. This conclusion is supported by the
many other extracted parameters. The lowest viscosity
was found in the base alloy, Mg65Cu25Gd10, in the level
of 106~107 Pa.s. Thus, even with much higher hardness,
the B- or Ag-additive Mg based BMG will be more
difficult to be formed, which appears to be a negative
factor in applying in the micro-forming or
nano-imprinting industry.
With the relatively low viscosity between 106~107
Pa.s within the supercooled temperature region of the
Mg58Cu31Y6Nd5 BMG, a high plastic strain can be
obtained easily by compression test within this
temperature region. In addition, the XRD result shows
that the Mg58Cu31Y6Nd5 BMG sample maintains its
amorphous state after compression at 458 K and different
strain rates. In parallel, a strain rate sensitivity exponent |
(m) close to 1.0 can be obtained for Mg58Cu31Y6Nd5
deformed at 448 K, 453 K and 458 K, suggesting an
ideal Newtonian fluid superplasticity behavior. A 6 mm
Mg58Cu31Y6Nd5 BMG rod was extruded at 458 K into a
long wire for more than 160 mm in length, as depicted in
Fig. 17 [90].
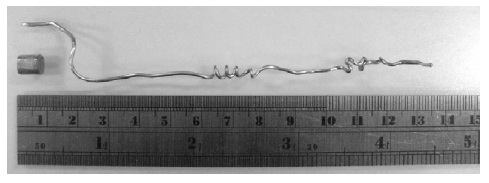
Fig. 17 A Mg58Cu31Y6Nd5 metallic glass wire with
dimension of 1 mm in diameter and a length more than
160 mm fabricated by extruding the 6 mm diameter
BMG rod at 458 K [90].
10. Forming and Application
Extensive plasticity (or superplasticity) of BMGs
at temperatures within the supercooled liquid region has
been studied extensively [91-94]. The alloys studied
included the Pd, Zr, Cu, and Ce based BMGs. The
superplastic-like behavior confirmed in the supercooled
liquid region can be used to process imprints of nanoand
micro-parts. A typical example is presented in Fig.
18 [95] for nano-grating using a Pd-based BMG. It is
demonstrated that nanostructured gratings with 600-nm
and 1500-nm periods can be replicated with high fidelity
on BMG in air using master Si dies. The grating features
and diffraction properties of the first-generation BMG
gratings are comparable to those of the original Si master
dies, but the quality of replica depends on the feature size
[95]. These replicated BMG gratings can be used as
molding dies to further create the second-generation
replicas on conventional polymethylmethacrylate
(PMMA). This study shed lights on the possibility of
nano-imprinting optical gratings on BMG in air and is a
first step towards fabrication of integrated optical
components such as diffractive optical nanostructured
elements.
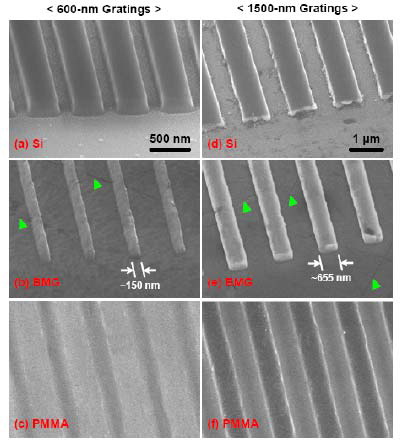
Fig. 18 SEM micrographs of the 600-nm (a,b,c) and
1500-nm (d,e,f) gratings in tilted view. The feature
widths of 600-nm and 1500-nm Pd40Ni40P20 BMG
gratings are (b) ~150 nm and (e) ~655 nm, respectively.
Green arrows indicate the polishing marks in BMG [95]. |
Potential application of the Zr based BMG can be
extended to the medical tool such as the surgical razor or
micro-surgery scissors. Because the razor made by the Zr
BMG presents much smoother edge than the razor made
by martensitic stainless steel. One example is shown in
Fig. 19 [96].
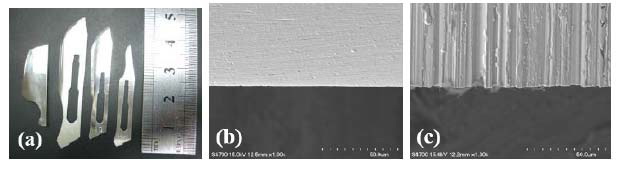
Fig. 19 (a) Appearance of Zr-based BMG razor and
commercial surgical razor. Enlarged knife edge of the
blade: (b) Zr-based BMG blade and (c) commercial
S-15C blade [96].
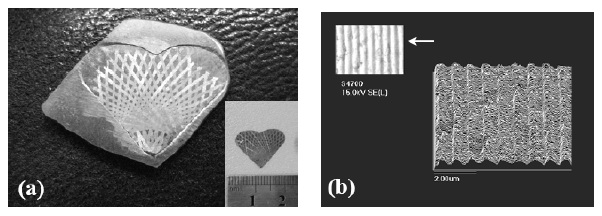
Fig. 20 The Mg58Cu31Y6Nd5 BMG photographs of (a)
pre-engraved die and imprinted hologram pattern at 458
K, (b) secondary electron image of SEM and surface
profile of the imprinted hologram pattern [90].
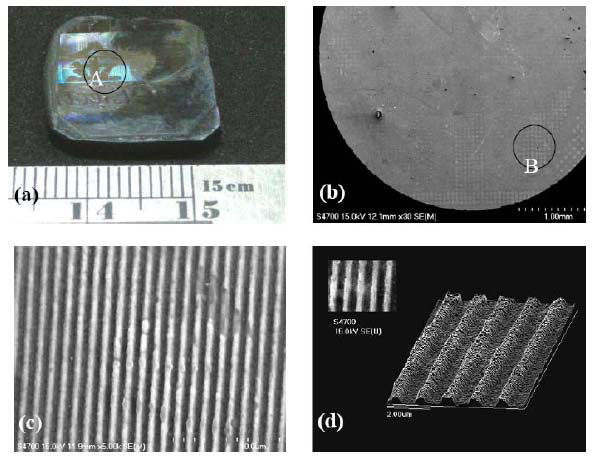
Fig. 21 (a) Photograph of imprinted hologram
pattern of the (Zr53Cu30Ni9Al8)99.5Si0.5 BMG, (b) SEM
images of circle A area in (a), (c) enlarges SEM image of
circle B area in (b), and (d) surface profile of the
imprinted hologram pattern [13].
Since both of the Zr based and Mg based BMGs
present superior viscous flow behavior within their
supercooled region. Therefore, these two BMGs can be
applied to duplicate the hologram pattern via a
micro-imprinting process. The replication of a hologram
pattern with 100 nm depth was replicated by the
Mg58Cu31Y6Nd5 BMG plate in the supercooled
temperature region (Fig. 20) [90]. In addition, an
imprinted hologram pattern with 0.6 μm depth also
demonstrates extremely good microforming ability of the
(Zr53Cu30Ni9Al8)99.5Si0.5 BMG, as shown in Fig. 21 [13].
The other attractive aspect in using BMGs for
micro-forming is the relatively low forming temperature. |
The Mg [97-100] and Au based BMGs [100] have low
glass transition temperatures in the range of 140-160oC,
making the viscous forming or imprinting easy to operate.
The low forming temperature lies in the same
temperature range for polymer materials such as PMMA,
and the low forming temperature also prevent from the
oxidation problem. The pressing can also be performed
in air due to the low forming temperatures within
140-160oC for the Mg and Au based BMGs. Successful
micro-imprinting of the Mg58Cu31Y11 BMGs have
achieved for making hexagonal micro-lens arrays. The
original convex Ni-Mo mold made by electro-plating is
pressed onto the BMG at 140-160oC for a few minutes at
a low pressure in the range 0.1 to 1 MPa (Fig. 22(a) [98]).
And the printed concave BMG mold is applied onto
PMMA, forming a convex pattern. The results
demonstrate that the imprinting is feasible and promising.
The resulting hexagonal micro-lens arrays are shown in
Fig. 22(b) [98]. Micro-scaled V-grove patterns (Fig. 22(c)
[98]) can also be imprinted on the Mg [97-99] and Au
based BMGs [100]. With the anti-oxidation,
anti-corrosion, and good forming ability, the Au based
BMG may be a material with high potential for micro
electro mechanical systems (MEMS) applications.
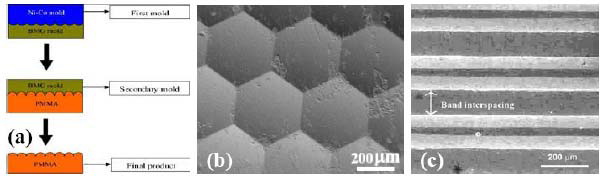
Fig. 22 (a) The schematic replication process first on
BMG and then on the PMMA, (b) SEM micrograph
showing the imprinted micro-lens, and (c) SEM
micrograph showing the V-groove pattern [98].
Acknowledgments
The authors gratefully acknowledge the long-term
sponsorship by National Science Council of Taiwan,
ROC, under the projects NSC 94-2218-E-110-009, NSC
95-2218-E-110-006, NSC 96-2218-E-110-001, NSC
95-2221-E-011-224-MY3, NSC 96-2628-E-011-117-
MY3, etc. The authors gratefully acknowledge the
collaboration with the USA team, Dr. C. T. Liu in Oak
Ridge National Laboratory and University of Tennessee,
Prof. Y. A. Chang in University of Wisconsin, Madison,
Prof. T. G. Nieh in University of Tennessee (formerly in
Lawrence Livermore National Laboratory), and Prof. P.
K. Liaw in University of Tennessee. The authors also
expressed their gratitude to their other local Taiwan team
members, Prof. K. C. Hsieh in National Sun Yat-Sen
University, Profs. P. Y. Lee, W. Kai and J. K. Wu in
National Ocean University and Tatung University, Prof.
C. Y. A Tsao in National Cheng Kung University, as well
as many devoted post-doctors and graduate students.
Thanks are due to Dr. C. T. Liu and Prof. K. L. Lin (of
NSC) who strongly promoted this international
collaboration projects.
References
[1] A. Inoue, “Stabilization of Metallic Supercooled Liquid
and Bulk Amorphous Alloys”, Acta Mater., 48 (2000) 279.
[2] W. H. Wang, C. Dong, C. H. Shek, “Bulk Metallic
|
Glasses”, Mater. Sci. Eng. R, 44 (2004) 45.
[3] J. Schroers, Q. Pham, A. Desai, “Themoplastic Forming of
Bulk Metallic Glass – A Technology for MEMS and
Microstructure Fabrication”, J. Microelectromechnical
Systems, 16 (2007) 240.
[4] M. W. Chen, “Mechanical Behavior of Metallic Glasses:
Microscopic Understanding of Strength and Ductility”,
Annul. Rev. Mater. Res., 38 (2008) 14.1.
[5] M. Miller and P. K. Liaw (ed), “Bulk Metallic Glasses, an
Overview”, Springer, NY, 2008.
[6] J. S. C. Jang, Y. W. Chen, L. J. Chang, H. Z. Cheng, J. C.
Huang, C. Y. Tsau, “Crystallization and Fracture Behavior
of the Zr65-xAl7.5Cu17.5Ni10Six Bulk Amorphous Alloys”,
Mater. Chem. Phys., 89 (2005) 122.
[7] J. S. C. Jang, L. J. Chang, G. J. Chen, and J. C. Huang,
“Crystallization Behavior of the Zr63Al7.5Cu17.5Ni10B2
Amorphous Alloy during Isothermal Annealing”,
Intermetallics, 13 (2005) 907.
[8] J. S. C. Jang, S. C. Lu, L. J. Chang, T. H. Hung, J. C.
Huang, C. Y. A. Tsao, “Crystallization and Thermal
Properties of Zr-Al-Cu-Ni Based Amorphous Alloy Added
with Boron and Silicon”, J. Metastable and
Nanocrystalline Mater., 24-25 (2005) 201.
[9] J. S. C. Jang, Y. W. Chen, L. J. Chang, H. Z. Cheng, J. C.
Huang, C. Y. A. Tsao, “Crystallization Kinetics of the
Zr61Al7.5 Cu17.5Ni10Si4 Alloy Using Isothermal DSC and
TEM Observation” J. Noncrystalline Solids, 352 (2006)
71.
[10] J. S. C. Jang, S. C. Lu, L. J. Chang, T. H. Yang, J. C.
Huang, C. T. Liu, “Thermal Stability and Crystallization
of Zr-Al-Cu-Ni Based Amorphous Alloy Added with
Boron and Silicon”, Intermetallics, 14 (2006) 951.
[11] T. H. Hung, J. C. Huang, J. S. C. Jang, S.C. Lu, “Improved
Thermal Stability of Amorphous ZrAlCuNi alloys with Si
and B”, Mater. Trans., 48 (2007) 239.
[12] L. J. Chang, I. H. Wang, J. S. C. Jang, G. J. Chen, T. H.
Hung, J. C. Huang, “Crystallization Kinetics and Thermal
Stability of the Zr60Al7.5 Cu17.5Ni10Si4B1 Alloy by
Isothermal DSC and TEM Observation”, Mater. Sci. Eng.
A, 449-451 (2007) 511.
[13] J. S. C. Jang, C. F. Chang, Y. C. Huang, J. C. Huang, W. J.
Chiang, C. T. Liu, “Viscous Flow and Microforming of a
Zr-Base Bulk Metallic Glass”, Intermetallics, accepted,
2008.
[14] Z. P. Lu, J. Shen, D. W. Xing, J. F. Sun, C. T. Liu, Appl.
Phys. Lett., 89 (2006) 071910.
[15] L. J. Chang, J. S. C. Jang, B. C. Yang, J. C. Huang,
“Crystallization and Thermal Stability of the Amorphous
Mg65Cu25-xGd10Agx (x=0 ~ 10) Alloys”, J. Alloy and
Compounds, 434-435 (2007) 221.
[16] T. H. Hung, Y. C. Chang, Y. N. Wang, C. W. Tang, H. M.
Chen, Y. L. Tsai, J. C. Huang, J. S. C. Jang, C. T. Liu,
“Development of Mg Based Amorphous Alloys with
Higher Amounts of Rare Earth Elements”, Mater. Trans.,
48 (2007) 1621.
[17] J. S. C. Jang, C. C. Tseng, L. J. Chang, C. F. Chang, W. J.
Lee, J. C. Huang, C. T. Liu, “Glass Forming Ability and
Thermal Properties of the Mg Based Amorphous Alloys
with Dual Rare Earth Elements Addition”, Mater. Trans.,
48 (2007) 1684.
[18] L. J. Chang, B. C. Yang, P. T. Chiang, J. S.C. Jang, J. C.
Huang, “Glass Forming and Thermal Properties of the
Mg65Cu25Gd10-xNdx (x=0~10) Amorphous Alloys”, Mater.
Sci. Forum, 539-543 (2007) 2106.
[19] Y. T. Cheng, T. H. Hung, J. C. Huang, J. S. C. Jang, Chi C.
Y. Tsao, P. Y. Lee, “Effects of Partial Replacement of Cu
and Y by Boron in Mg-Cu-Y Amorphous Alloys”,
Intermetallics, 14 (2006) 866.
[20] Y. T. Cheng, T. H. Hung, J. C. Huang, P. J. Hsieh, J. S. C. |
Jang, “The Thermal Stability and Crystallization Kinetics
of Mg-Cu-Y-B Alloys”, Mater. Sci. Eng. A, 449-451 (2007)
501.
[21] X. H. Du, J. C. Huang, K. C. Hsieh, J. S. C. Jang, P. K.
Liaw, Y. H. Lai, H. M. Chen, “Two-Glassy-Phase Bulk
Metallic Glass with Remarkable Plasticity”, Appl. Phys.
Lett., 91 (2007) 131901.
[22] X. H. Du, J. C. Huang, K. C. Hsieh, J. S. C. Jang, P. K.
Liaw, “Mechanical Properties of Zr-Based Two-Glassy
Phase Bulk Metallic Glass”, accepted by Adv. Eng. Mater.,
2008.
[23] X. H. Du, J. C. Huang, H. M. Chen, H. S. Chou, Y. H. Lai,
K. C. Hsieh, J. S. C. Jang, P. K. Liaw, “Phase Separated
Microstructure and Shear Banding Behavior in a Designed
Zr Based Glass-Forming Alloy”, submitted to
Intermetallics, 2008.
[24] T. Zhang, A. Inoue, T. Masumoto, Mater. Trans. JIM, 32
(1991) 1005.
[25] X. H. Du, J. C. Huang, “A Modified Glass Formation
Criterion for Various Glass Forming Liquids with Higher
Reliability”, Chinese Phys. Lett., 24 (2007) 1335.
[26] X. H. Du, J. C. Huang, C. T. Liu, Z. P. Lu, “New Criterion
of Glass Forming Ability for Bulk Metallic Glasses”, J.
Appl. Phys., 101 (2007) 086108.
[27] X. H. Du, J. C. Huang, “New Criterion in Predicting Glass
Forming Ability of Various Glass-Forming Systems”,
Chinese Phys. B, 17 (2008) 249.
[28] C. Y. Lin, H. Y. Tien, T. S. Chin, “Soft Magnetic Ternary
Iron-Boron Based Bulk Metallic Glasses”, Appl. Phys.
Lett., 86 (2005) 162501.
[29] M. C. Lee, C. Y. Lin, T. S. Chin, “High Permeability
Nano-Crystalline FeSiBTaAg Ribbons Obtained by Direct
Casting”, Intermetallics, 15 (2007) 1564.
[30] H. Y. Tien, C. Y. Lin, T. S. Chin, “New Ternary Ni-Ta-Sn
Bulk Metallic Glasses”, Intermetallics, 14 (2006) 1075.
[31] L. R. Chang, J. H. Young, J. S. C. Jang, J. C. Huang, Chi Y.
A. Tsao, “Synthesis of the Magnesium-Based
Nano/Amorphous-Composite Alloy Powder by the
Combination Method of Melt-Spinning and Mechanical
Alloying”, Key Eng. Mater., 313 (2006) 97.
[32] J. S. C. Jang, L. J. Chang, J. H. Young, J. C. Huang, Chi
Y.A. Tsao, “Synthesis and Characterization of the
Mg-Based Amorphous/Nano ZrO2 Composite Alloy”,
Intermetallics, 14 (2006) 945.
[33] L. J. Chang, J. H. Young, J. S. C. Jang, J. C. Huang, Chi
Y.A. Tsao, “Mechanical Properties of the Mg-Based
Amorphous Zincornia Composite Alloy”, Mater. Sci.
Forum, 539-543 (2007) 925.
[34] L. J. Chang, G. R. Fang, J. S. C. Jang, I. S. Lee, J. C.
Huang, Chi Y. A. Tsao, “Hot Workability of the
Mg65Cu20Y10Ag5 Amorphous/NanoZrO2 Composite Alloy
within Supercooled Temperature Region”, Key Eng.
Mater., 351 (2007) 103.
[35] L. R. Chang, G. R. Fang, L. S. Lee, J. S. C. Jang, J. C.
Huang, Chi Y. A. Tsao, “Mechanical Properties of the Hot
Pressed Mg65Cu20Y10Ag5/Nano-ZrO2 Based Amorphous
Matrix Composites”, Mater. Trans., 48 (2007) 1797.
[36] M. L. Ted Guo, Chi Y. A. Tsao, J. C. Huang, J. S. C. Jang,
“Crystallization Behavior of Spray-Formed and Melt-Spun
Al89La6Ni5 Hybrid Composites with Amorphous and
Nanostructured Phases”, Mater. Sci. Eng. A, 404 (2005)
49.
[37] M. L. Ted Guo, Chi Y. A. Tsao, J. S. C. Jang, J. C. Huang,
“Microstructure Evolution of Spray-Formed Bulk Hybrid
Composite and Melt-Spun Ribbon Hybrid Composite
Consisting of Amorphous and Nanostructured Phases of
Al89Nd4Ni5Cu2”, Intermetallics, 14 (2006) 1069.
[38] M. L. T. Guo, Chi Y. A. Tsao, J. C. Huang, J. S. C. Jang,
“Microstructure Characteristics of Spray-Formed and |
Melt-Spun Al85Nd5Ni10 and Al89La6Ni5 Bulk Hybrid
Composites”, Key Eng. Mater., 351 (2007) 1.
[39] M.-L. Ted Guo, Chi Y. A. Tsao, J. C. Huang, J. S. C. Jang,
“Thermal Stability and Mechanical Properties of
Spray-Formed Al89La6Ni5 Bulk Hybrid Composites with
Amorphous Matrix”, Mater. Trans., 48 (2007) 1717.
[40] K. F. Chang, M.-L. T. Guo, R. H. Kong, Chi Y.A. Tsao, J.
C. Huang, J. S. C. Jang, “Mg-Cu-Gd Layered Composite
Plate Synthesized via Spray Forming Process”, Mater. Sci.
Eng. A, 477 (2008) 58.
[41] P. Y. Lee, C. K. Lin, I. K. Jeng, C. C. Wang, G. S. Chen,
“Characterization of Ni57Zr20Ti18Al5 Amorphous Powder
Obtained by Mechanical Alloying”, Mater. Chem. Phys.,
84 (2004) 358.
[42] P. Y. Lee, C. J. Yao, J. S. Chen, L. Y Wang, R. R. Jeng, Y.
L. Lin, “Preparation and Thermal Stability of
Mechanically Alloyed Cu-Zr-Ti-YAmorphous Powders”,
Mater. Sci. Eng. A, 375-377 (2004) 834.
[43] C. K. Lin, C. C. Wang, R. R. Jeng, Y. L. Lin, C. H. Yeh, J.
P. Chu, P. Y. Lee, “Preparation and Thermal Stability of
Mechanically Alloyed Ni-Zr-Ti-Y Amorphous Powders”,
Intermetallics, 12 (2004) 1011.
[44] I. K. Jeng, P. Y. Lee, “Synthesis of Ti-Based Bulk
Metallic Glass Composites Containing WC Particles”,
Mater. Trans., 46 (2005) 2963.
[45] P. Y. Lee, C. Lo, J. S. C. Jang, J. C. Huang, “Mg-Y-Cu
Bulk Nanocrystalline Matrix Composites Containing WC
Particles”, Key Eng. Mater., 313 (2006) 25.
[46] P. Y. Lee, M. C. Kao, C. K. Lin, J. C. Huang, “Mg-Y-Cu
Bulk Metallic Glass Prepared by Mechanical Alloying and
Vacuum Hot-Pressing”, Intermetallics, 14 (2006) 994.
[47] P. Y. Lee, W. C. Liu, C. K. Lin, J. C. Huang, “Fabrication
of Mg-Y-Cu Bulk Metallic Glass by Mechanical Alloying
and Hot Consolidation”, Mater. Sci. Eng. A, 449-451
(2007) 1095.
[48] H. M. Wu, S. S. Hung, P. Y. Lee, “Characterization of
Ni57Zr20Ti20Sn3 Amorphous Powders Obtained by
Mechanical Alloying”, J. Alloys and Compounds, 434-435
(2007) 386.
[49] P. J. Hsieh, Y. P. Hung, J. C. Huang, “Transformation into
Nano-Grained or Amorphous State in Zr-X Binary
Systems by Accumulated Roll Bonding”, Scripta Mater.,
49 (2003) 173.
[50] P. J. Hsieh, Y. P. Hung, S. Y. Chiu, J. C. Huang,
“Nanocrystallization and Amorphization Mechanisms in
Zr-X Alloys during Accumulated Roll Bonding”, Mater.
Trans. (JIM), 45 (2004) 2686.
[51] P. J. Hsieh, J. C. Huang, Y. P. Hung, S. Y. Chiu, J. S. C.
Jang, “TEM Characterization of Nanocrystallization and
Amorphization Evolution in Zr-X Alloys during
Accumulated Roll Bonding”, Mater. Chem. Phys., 88
(2004) 364.
[52] P. J. Hsieh, J. C. Huang, J. S. C. Jang, C. Y. A. Tsao,
“Transformation between Nanocrystallines and
Amorphous Phases in Zr-X Alloys during Accumulative
Roll Bonding”, J. Metastable and Nanocrystalline Mater.,
24-25 (2005) 351.
[53] P. J. Hsieh, Y. C. Lo, J. C. Huang, S. P. Chu, “On the
Latest Stage of Transformation from Nanocrystalline to
Amorphous Phases durng ARB: Simulation and
Experiment”, Intermetallics, 14 (2006) 924.
[54] P. J. Hsieh, Y. C. Lo, C. T. Wang, J. C. Huang, S. P. Chu,
“Cyclic Transformation between Nanocrystalline and
Amorphous Phases in Zr Based Intermetallic Alloys
during ARB”, Intermetallics, 15 (2007) 644.
[55] Y. C. Lo, S. P. Ju, J. C. Huang, X. H. Du, “Atomic
Structural Evolution of Zr-Ni during Accumulative Roll
Bonding Using Honeycutt-Anderson (HA) Pair Analysis”,
Phys. Rev. B, 76 (2007) 024103. |
[56] Y. C. Lo, J. C. Huang, S. P. Ju, “Atomic Structure
Evolution of Zr-Ti and Pure Zr during Accumulated Roll
Bonding by HA Pair Analysis”, Mater. Chem. Phys., 2008
(on line).
[57] C. H. Chuang, J. C. Huang, P. J. Hsieh, “Using Friction
Stir Processing to Fabricate MgAlZn Intermetallic Alloys”,
Scripta Mater., 53 (2005) 1455.
[58] C. I. Chang, C. J. Lee, C. H. Chuang, H. R. Pei, J. C.
Huang, “On Mg-Al-Zn Intermetallic Alloys Made by
Friction Stir Processing Containing Quasi-Crystals and
Amorphous Phases”, Adv. Mater. Research, 15-17 (2007)
387.
[59] H. M. Chen, Y. C. Chang, T. H. Hung, J. C. Huang, J. S. C.
Jang, P. K. Liaw, “Compression Properties of Mg-Cu-Gd
Bulk Metallic Glasses with Various Specimen Height to
Diameter Ratios”, Mater. Trans., 48 (2007) 1802.
[60] C. J. Lee, J. C. Huang, T. G. Nieh, “Sample Size Effect on
the Mechanical Behavior of Mg65Cu25Gd10 Metallic
Glass”, Appl. Phys. Lett., 91 (2007) 161913.
[61] Y. H. Lai, C. J. Lee, Y. T. Cheng, H. M. Chen, H. S. Chou,
X. H. Du, C. I. Chang, J. C. Huang, S. R. Jain, J. S. C.
Jang, T. G. Nieh, “Bulk and Microscale Compressive
Properties of Zr-Based Metallic Glass”, Scripta Mater. 58
(2008) 890.
[62] C. W. Tang, MS thesis, National Sun Yat-Sen University,
Kaohsiung, Taiwan, 2008.
[63] W. F. Wu, Y. Li, C. A. Schuh, Philos. Mag. 88 (2008) 71.
[64] J. S. C. Jang, J. Y. Ciou, T. H. Hung, J. C. Huang, X. H.
Du, “Enhanced Mechanical Performance of Mg Based
Metallic Glass with Porous Mo Particles”, Appl. Phys.
Lett., 92 (2008) 011930.
[65] J. S. C. Jang, T. H. Li, L. J. Chang, J. C. Huang, Chi Y. A.
Tsao, S. R. Jian, “Plasticity Enhancement of Mg-Based
Bulk Metallic Glass with Ductile Fe Particles”, submitted
to Mater. Chem. Phys., 2008.
[66] J. S. C. Jang, J. C. Huang, X. H. Du, “Plasticity
Enhancement of Mg-Based Bulk Metallic Glass with
Ductile Ta Particles”, unpublished research, 2008.
[67] J. D. Honeycutt, H. C. Andersen, J. Phys. Chem. 91 (1987)
4950.
[68] J. P. Chu, C. T. Liu, S. F. Wang, T. Mahalingam, M. J.
O’Keefe, B. Johnson, C. H. Kuo, “Annealing-Induced Full
Amorphization in a Multicomponent Metallic Film,” Phys.
Rev. B, 69 (2004) 113410.
[69] J. P. Chu, C. T. Lo, Y. K. Fang, B. S. Han, “On
Annealing-Induced Amorphization and Anisotropy in a
Ferromagnetic Fe-based Film: A Magnetic and Property
Study,” Appl. Phys. Lett., 88 (2006) 012510.
[70] C. L. Chiang, J. P. Chu, F. X. Liu, P. K. Liaw, R. A.
Buchanan, “A 200 nm Thick Glass-Forming Metallic Film
for Fatigue-Property Enhancements,” Appl. Phys. Lett., 88,
(2006) 131902.
[71] F. X. Liu, P. K. Liaw, W. H. Jiang, C. L. Chiang, Y. F. Gao,
Y. F. Guan, J. P. Chu, P. D. Rack, “Fatigue-Resistance
Enhancements by Glass-Forming Metallic Films,” Mater.
Sci. Eng. A, 468-470 (2007) 246.
[72] C. J. Chen, J. C. Huang, Y. H. Lai, H. S. Chou, L. W.
Chang, X. H. Du, J. P. Chu, T. G. Nieh, “On the
Amorphous and Nanocrystalline Zr-Cu and Zr-Ti
Sputtered Thin Films”, accepted by J. Alloys Compounds,
2008.
[73] H. S. Chou, J. C. Huang, L. W. Chang, T. G. Nieh, “Phase
Transformation and Nano-Indentation Response in
Zr-Cu-Ti Thin Films”, accepted by Appl. Phys. Lett.,
2008.
[74] H. S. Chou, J. C. Huang, Y. H. Lai, L. W. Chang, X. H. Du,
J. P. Chu, T. G. Nieh, “Amorphous and Nanocrystalline
Sputtered Mg-Cu Thin Films”, accepted by J. Alloys
Compounds, 2008. |
[75] H. H. Hsieh, W. Kai, R. T. Huang, C. Y. Lin, T. S. Chin,
“Air Oxidation of Fe72B22Y6 Bulk Amorphous Alloy at
600-700oC”, Intermetallics, 14 (2006) 917.
[76] W. Kai, H. H. Hsieh, Y. R. Chen, Y. F. Wang, C. Dong,
“Oxidation Behavior of an Zr53Ni23.5Al23.5 Bulk Metallic
Glass at 400-600°C”, Intermetallics, 15 (2007) 1459.
[77] W. Kai, H. H. Hsieh, T. H. Ho, R. T. Huang, Y. L. Lin,
“Air-Oxidation Behavior of a Cu60Hf25Ti15 Bulk Metallic
Glass at 375-520°C”, Oxidation of Metals, 68 (2007) 177.
[78] H. H. Hsieh, W. Kai, W. L. Jang, R. T. Huang, P. Y. Lee, W.
H. Wang, “The Oxidation Behavior of Cu-Zr-Ti-Base
Bulk Metallic Glasses in air at 350-500°C”, Oxidation of
Metals, 67 (2007) 179.
[79] W. Kai, T. H. Ho, I. F. Jen, P. Y. Lee, Y. M. Yang, T. S.
Chin, “Oxidation Behavior of the (Cu78Y22)98Al2 Bulk
Metallic Glass Containing Cu5Y-Particle Composite at
400-600°C”, Intermetallics, 16 (2008) 629.
[80] W. Kai, T. H. Ho, H. H. Hsieh, Y. R. Chen, D. C. Qiao, F.
Jiang, G. Fan, P. K. Liaw, “Oxidation Behavior of
CuZr-based Glassy Alloys at 400-500°C in Dry Air”,
Metall. Mater. Trans., A, 39 (2008) 1838.
[81] H. H. Hsieh, W. Kai, R. T. Huang, D. C. Qiao, P. K. Liaw,
“Air Oxidation of an Fe48Cr15C15MO14B6Er2 Bulk Metallic
Glass at 600-725°C”, Mater. Trans., 48 (2007) 1864.
[82] H. H. Hsieh, W. Kai, C. Y. Lin, T. S. Chin, “Oxidation
Behavior of the Y56Al24Co20 Bulk Amorphous Alloy
Containing Crystalline Composites at 325-450oC”, Mater.
Sci. Forum, 539-543 (2007) 2117.
[83] Y. F. Wu, W. C. Chiang, J. K. Wu, “Effect of
Crystallization on Corrosion Behavior of F40Ni38B18Mo4
Amorphous Alloy in 3.5% NaCl Solution”, Mater. Lett.,
62 (2008) 1554.
[84] Y. F. Wu, W. C. Chiang, J. P. Chu, T. G. Nieh, Y.
Kawamura, J. K. Wu, “Corrosion Resistance of
Amorphous and Crystalline Pd40Ni40P20 Alloys in Aqueous
Solutions”, Mater. Lett., 60 (2006) 2416.
[85] W.C. Chiang, W. D. Yeh, J. K. Wu, ‘Hydrogen Permeation
in Fe40Ni38B18Mo4 and Fe81B13.5Si3.5C2 Amorphous
Alloys”, Mater. Lett., 59 (2005) 2542.
[86] H. M. Lin, J. K. Wu, C. C. Wang, P. Y. Lee, “The
Corrosion Behavior of Mechanically Alloyed Cu-Zr-Ti
Bulk Metallic Glasses”, Mater. Lett., 62 (2008) 2995.
[87] Y. C. Chang, T. H. Hung, H. M. Chen, J. C. Huang, T. G.
Nieh, C. J. Lee, “Viscous Flow Behavior and Thermal
Properties of Bulk Amorphous Mg58Cu31Y11 Alloy”,
Intermetallics, 15 (2007) 1303.
[88] Y. C. Chang, J. C. Huang, Y. T. Cheng, C. J. Lee, X. H. Du,
T. G. Nieh, “Effect of Silver or Boron on Viscosity and
Thermomechanical Properties in Mg-Cu-Gd Metallic
Glasses”, J. Appl. Phys., 103 (2008) 103521.
[89] Y. C. Chang, C. W. Tang, J. C. Huang, T. G. Nieh,
“Viscous Flow Behavior and Workability of
Mg-Cu-(Ag)-Gd Based Bulk Metallic Glasses”, accepted
by Mater. Trans., 2008.
[90] J. S. C. Jang, C. T. Tseng, L. J. Chang, J. C. Huang, Y. C.
Yeh, J. L. Jou , “Thermoplastic Forming Properties and
Microreplication Ability of a Mg-Based Bulk Metallic
Glass”, Adv. Eng. Mater., in press, 2008.
[91] J. P. Chu, C. L. Chiang, T. G. Nieh, Y. Kawamura,
“Superplasticity in a Bulk Amorphous Pd40Ni40P20 Alloy:
A Compression Study,” Intermetallics, 10 (2002) 1191.
[92] J. P. Chu, C. L. Chiang, T. Mahalingam, T. G. Nieh,
“Plastic Flow and Tensile Ductility of a Bulk Amorphous
Zr55Al10Cu30Ni5 Alloy at 700 K,” Scripta Mater., 49 (2003)
435.
[93] C. L. Chiang, J. P. Chu, C. T. Lo, T. G. Nieh, Z. X. Wang,
W. H. Wang, “Homogeneous Plastic Deformation in a
Cu-Based Bulk Amorphous Alloy,” Intermetallics, 12
(2004) 1057. |
[94] J. P. Chu, C. L. Chiang, H. Wijaya, R. T. Huang, C. W. Wu,
B. Zhang, W. H. Wang, T. G. Nieh, “Compressive
Deformation of a Bulk Ce-Based Metallic Glass,” Scripta
Materialia, 55 (2006) 227.
[95] J. P. Chu, H. Wijaya, C. W. Wu, T. R. Tsai , C. S. Wei, T. G.
Nieh, J. Wadsworth, “Nanoimprint of Gratings on a Bulk
Metallic Glass,” Appl. Phys. Lett., 90 (2007) 034101.
[96] J. S. C. Jang, unpublished research work, I-Shou
University, Kaohsiung, Taiwan, 2008.
[97] C. T. Pan, T. T. Wu, Y. C. Chang, J. C. Huang,
“Experiment and Simulation of Hot Embossing of a Bulk
Metallic Glass with Low Pressure and Temperature”, J. of
Micromechanics and Microengineering, 18 (2008)
025010.
[98] C. T. Pan, T. T. Wu, M. F. Chen, Y. M. Hwang, Y. C.
Chang, C. J. Lee, J. C. Huang, “Hot Embossing of
Micro-Lens Array on Bulk Metallic Glass”, Sensors and
Actuators A: Physical, 141 (2008) 422.
[99] Y. C. Chang, T. T. Wu, M. F. Chen, C. J. Lee, J. C. Huang,
C. T. Pan, “Finite Element Simulation of Micro-Imprinting
in Mg-Cu-Y Amorphous Alloy”, Mater. Sci. Eng. A, 2008
(on line).
[100] C. W. Tang, Y. C. Chang, T. T. Wu, J. C. Huang, C. T. Pan,
“Micro-Forming of Au49Ag5.5Pd2.3Cu26.9Si16.3 Metallic
Glasses in Supercooled Region”, Adv. Mater. Research,
47-50 (2008) 266. |
Review article (可點選連結以下載本文)
Thin Film Metallic Glasses: Preparations, Properties, and Applications
J.P. Chu, J.C. Huang, J.S.C. Jang, Y.C. Wang, and P.K. Liaw
(J.O.M., vol. 62, No. 4, 2010, pp. 19-24.)
|
|
|
|
|
|
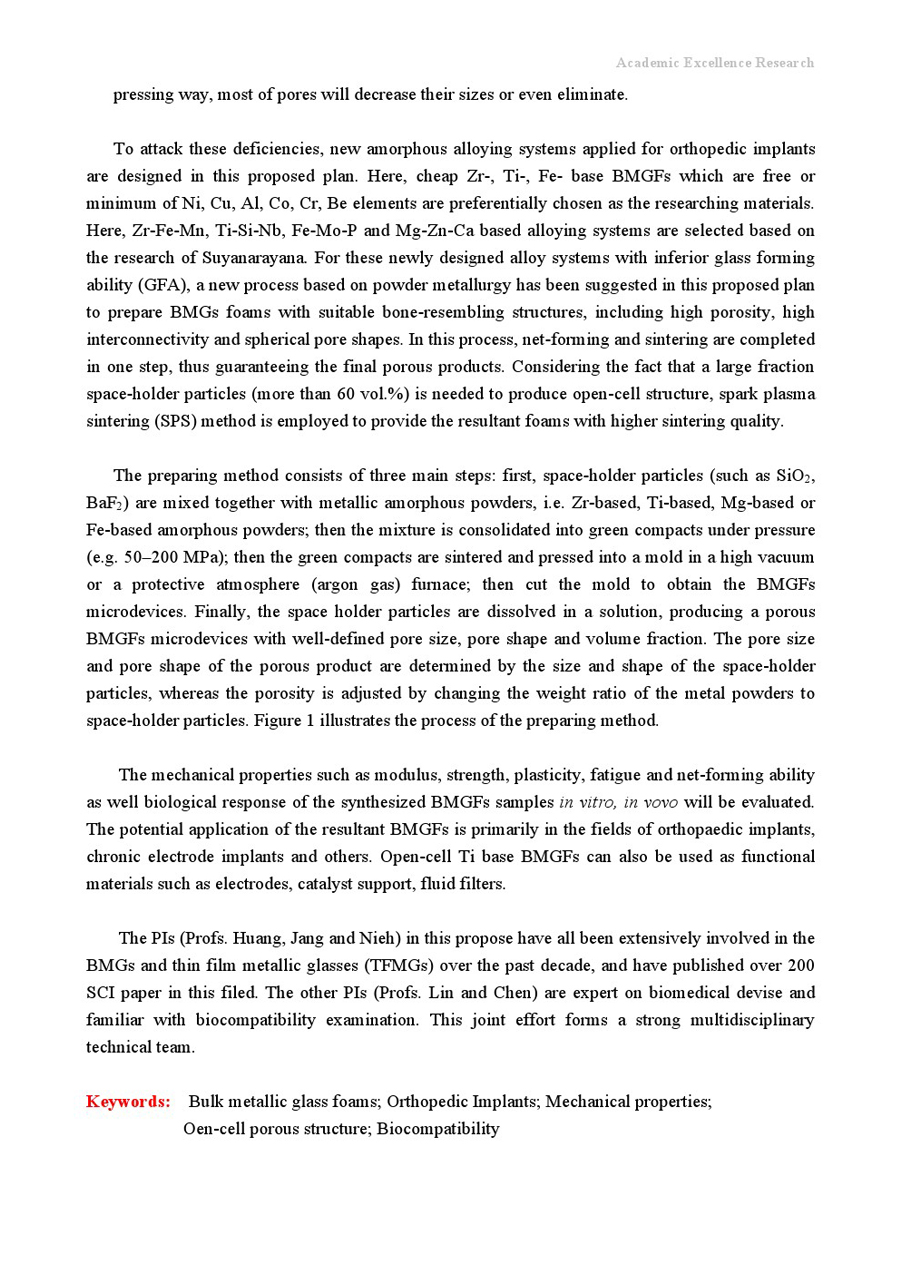
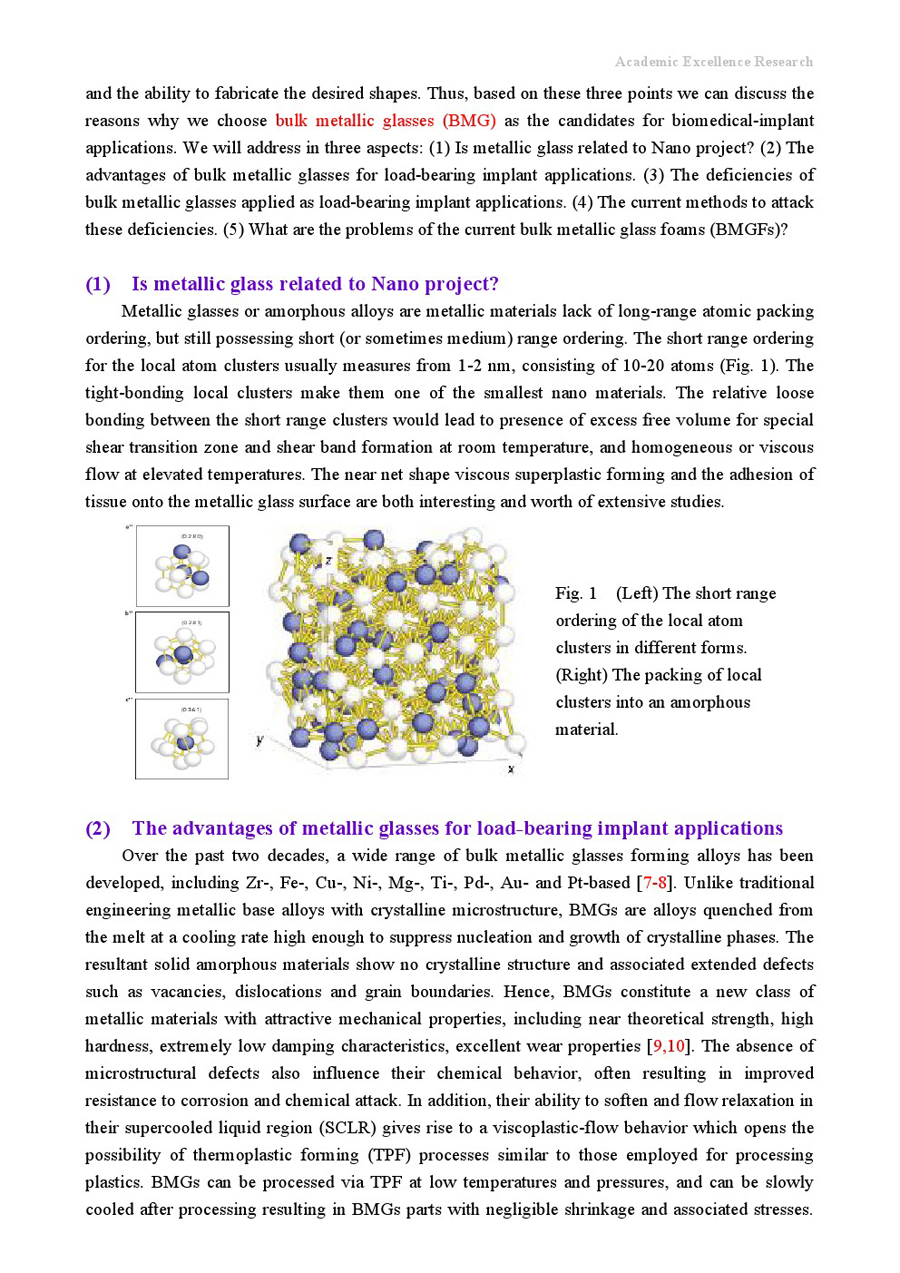
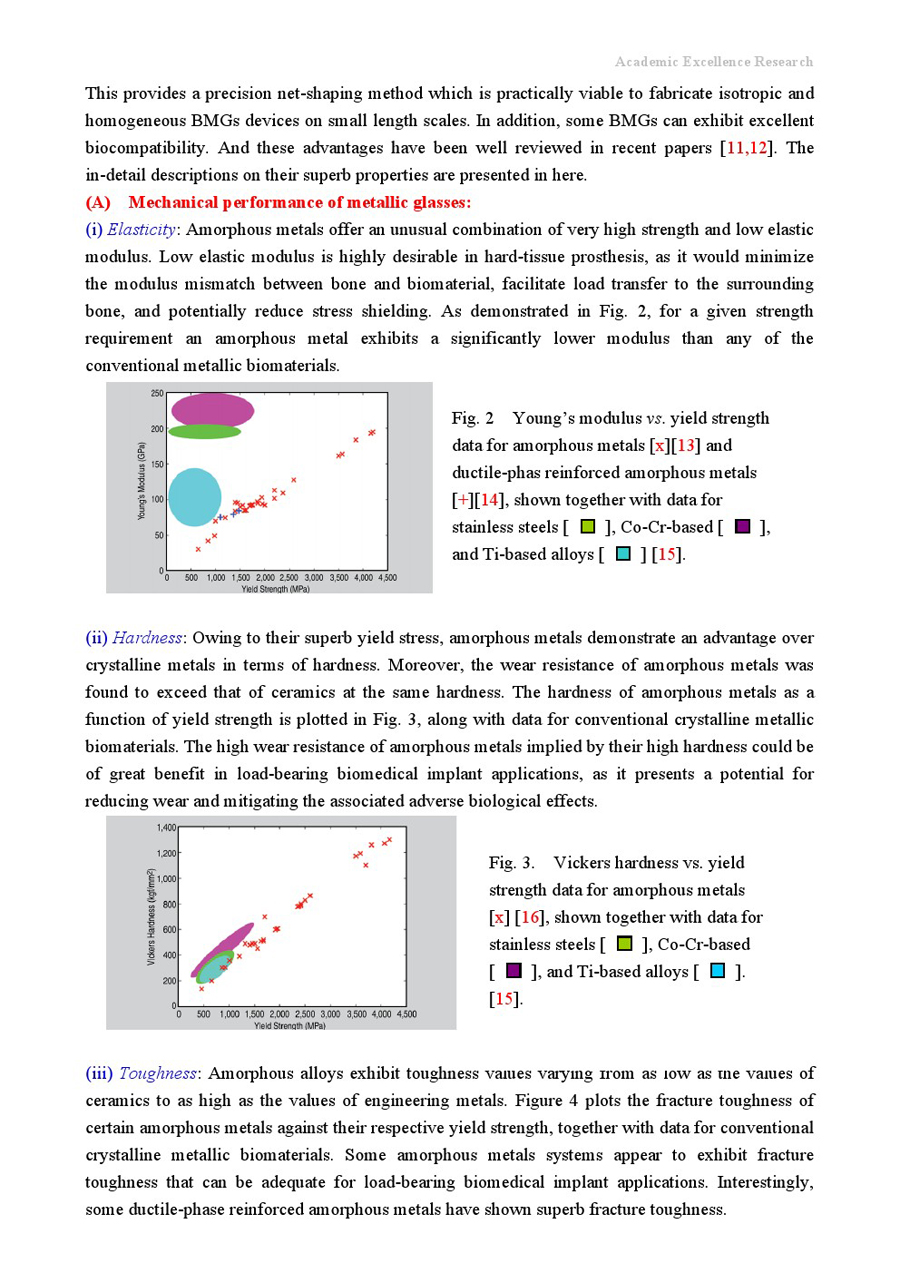 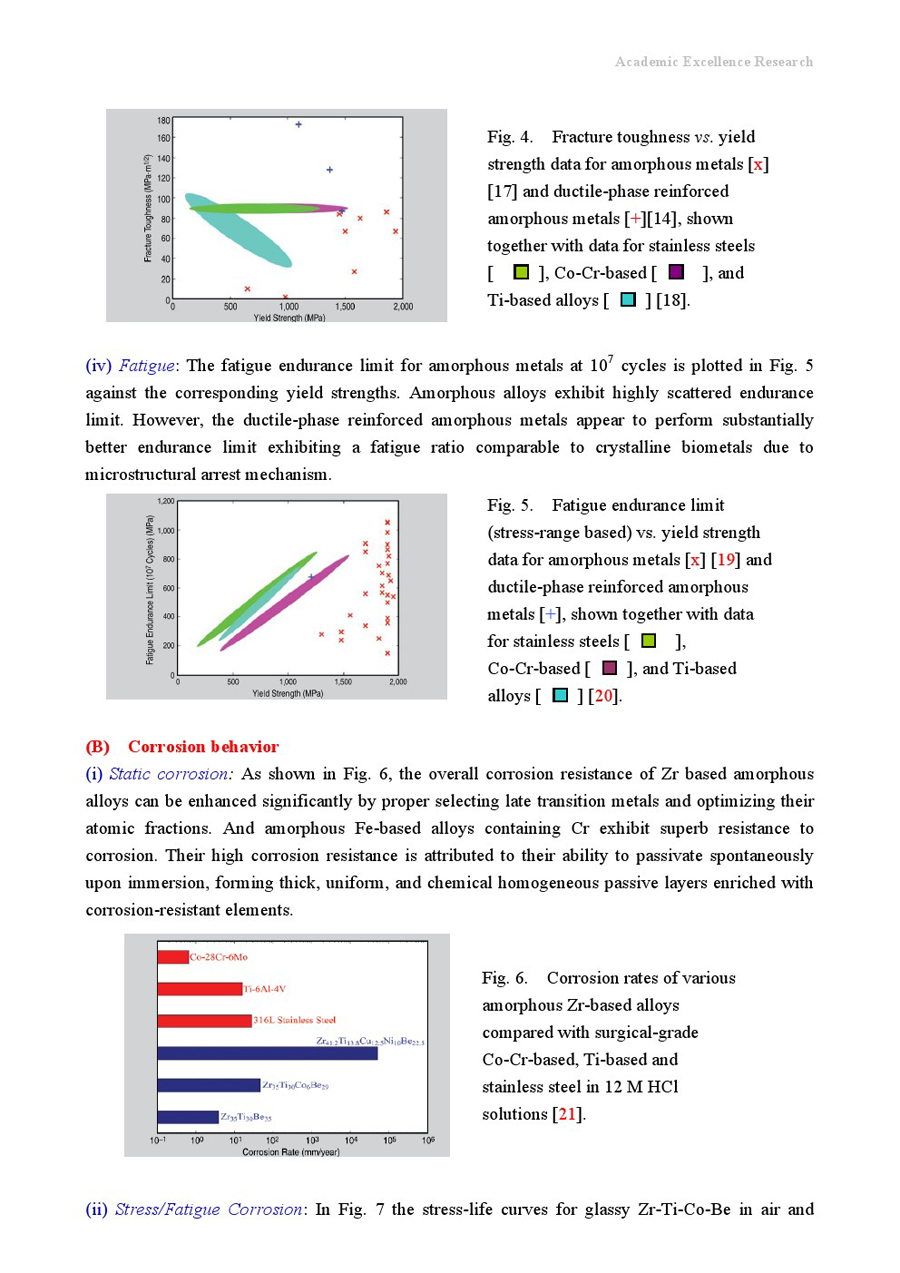 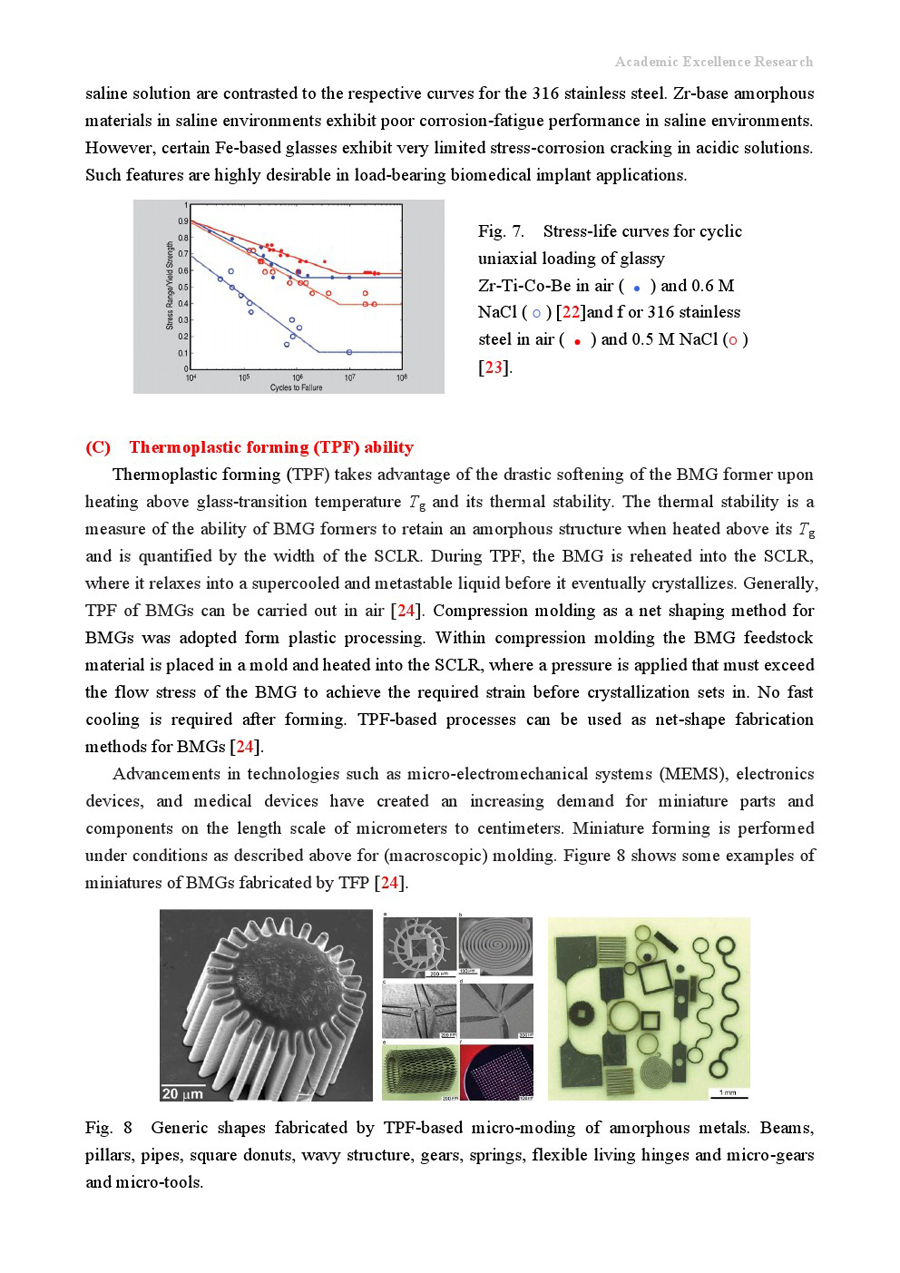 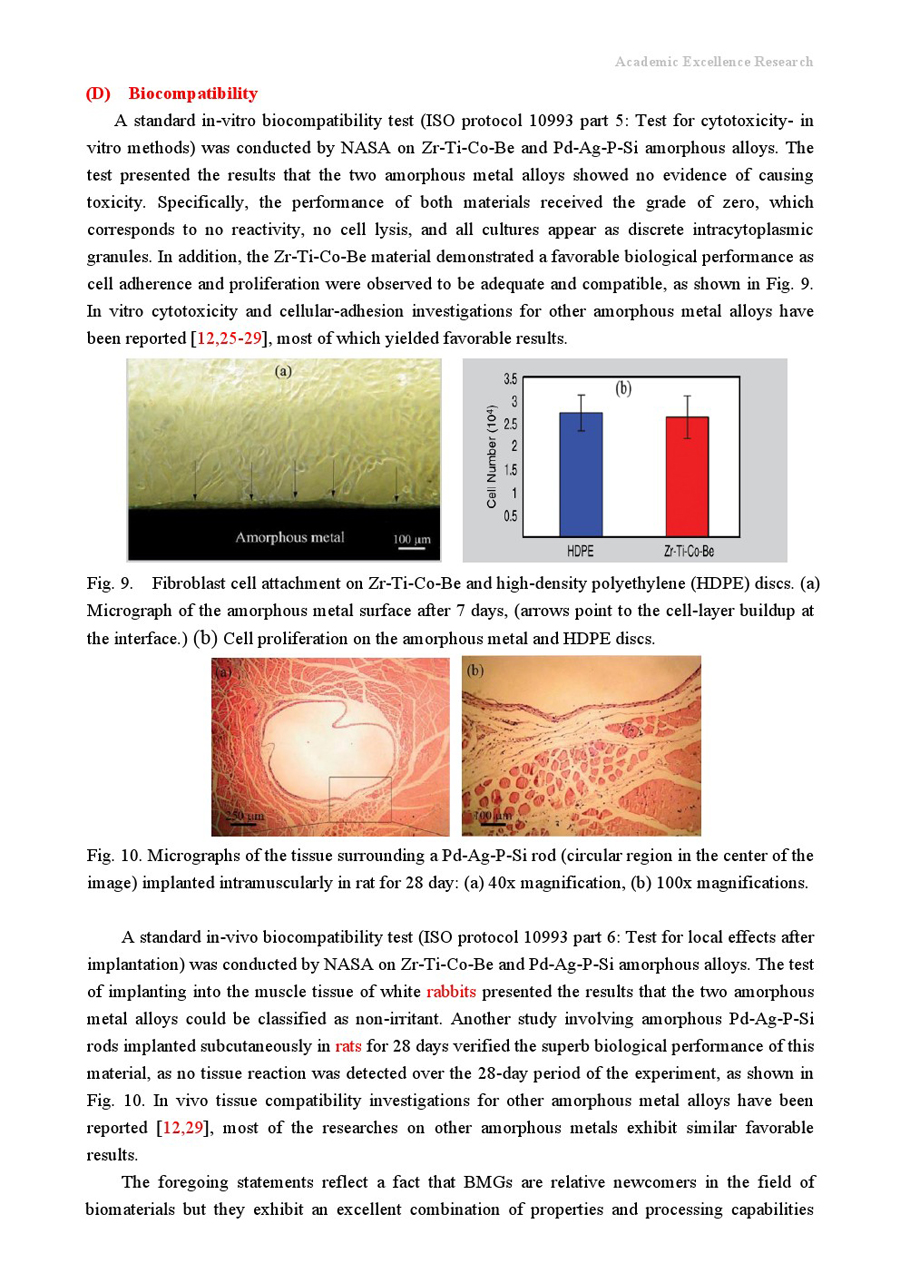 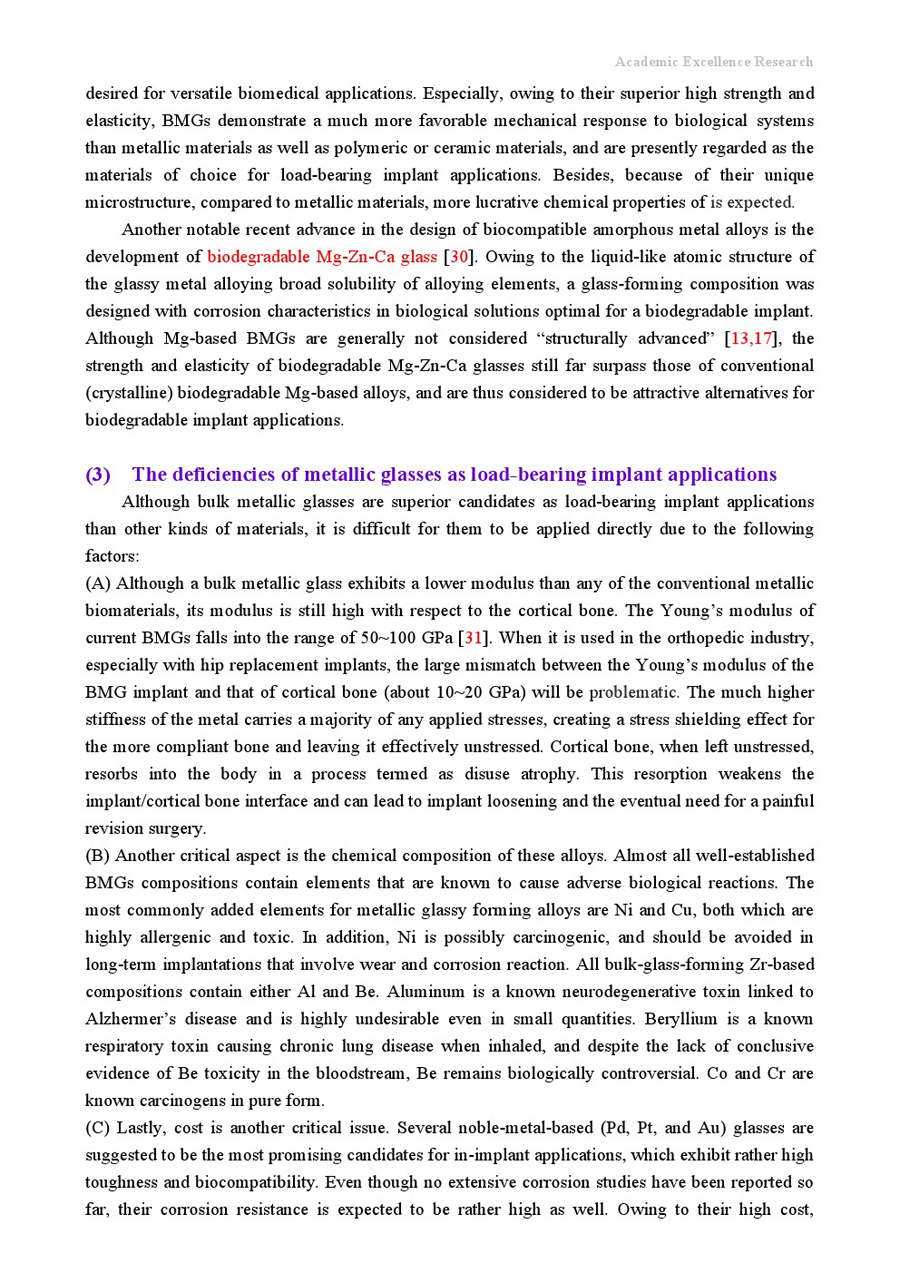 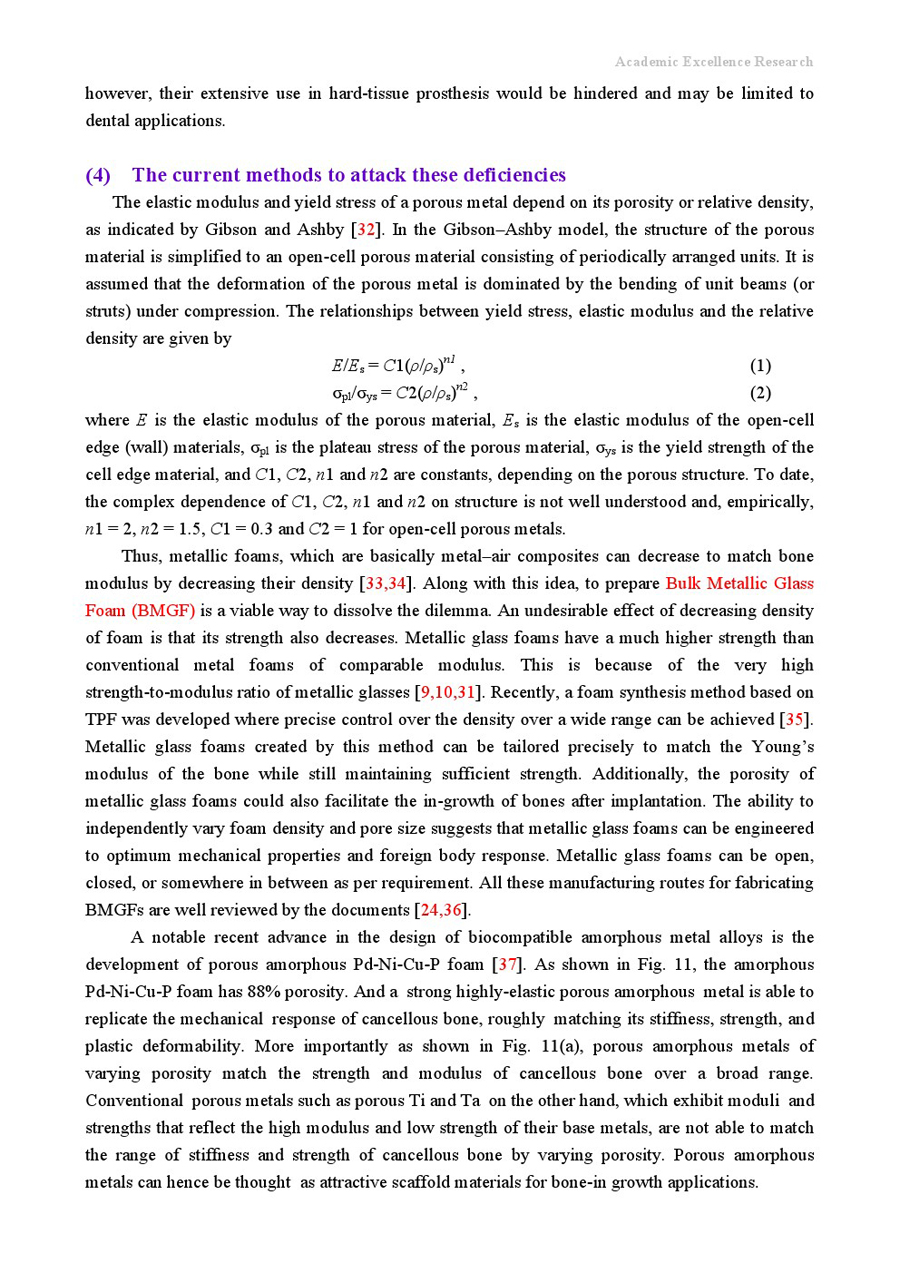 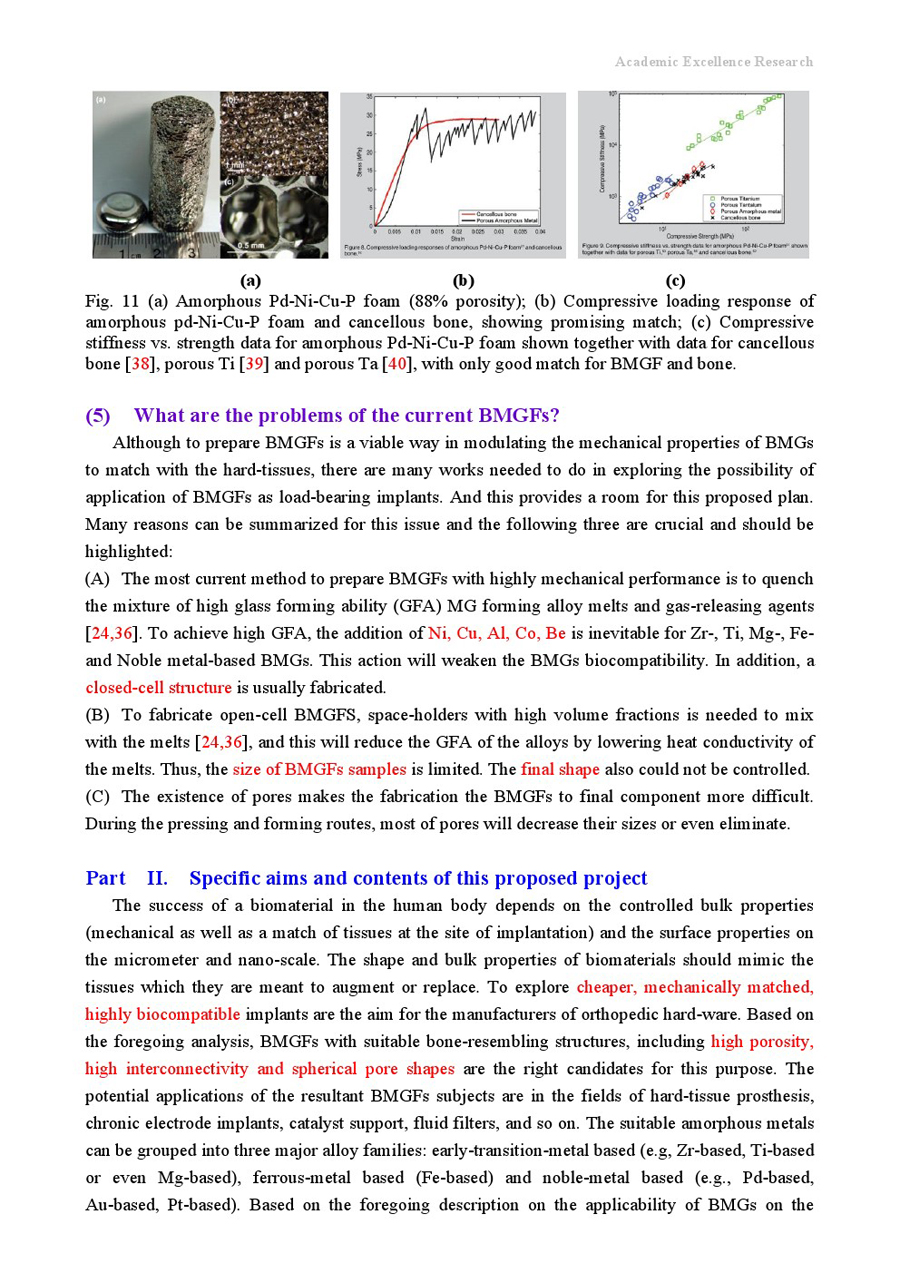 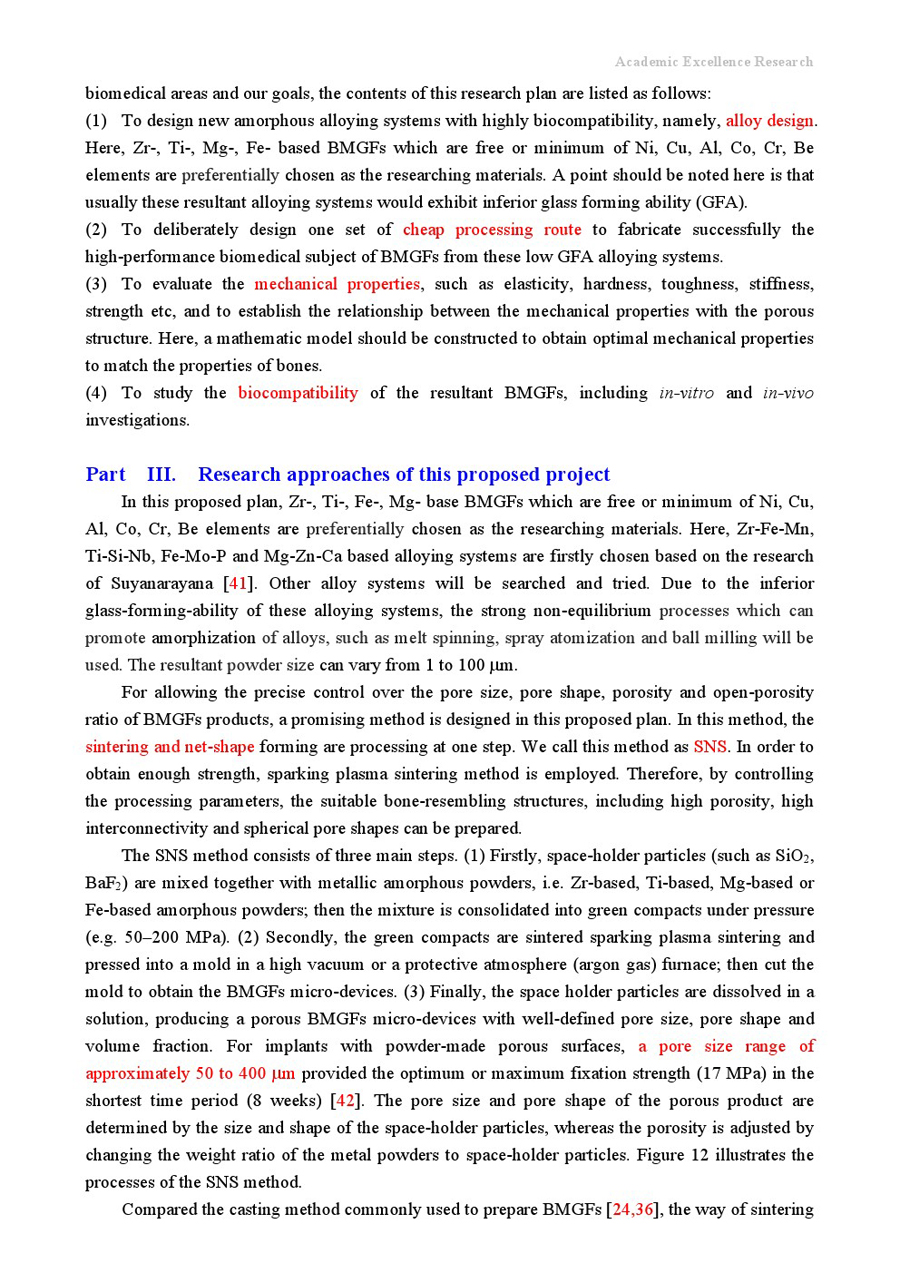 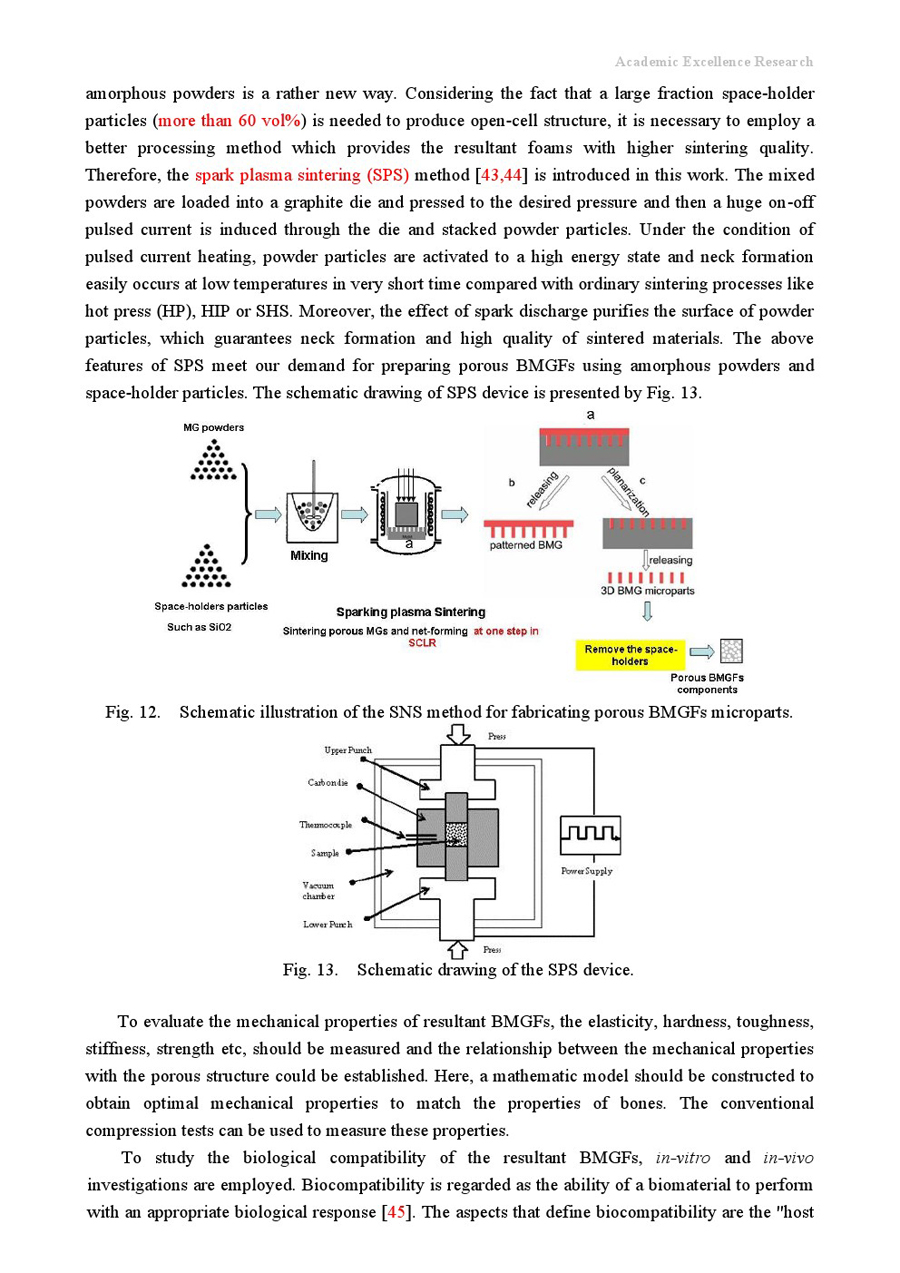 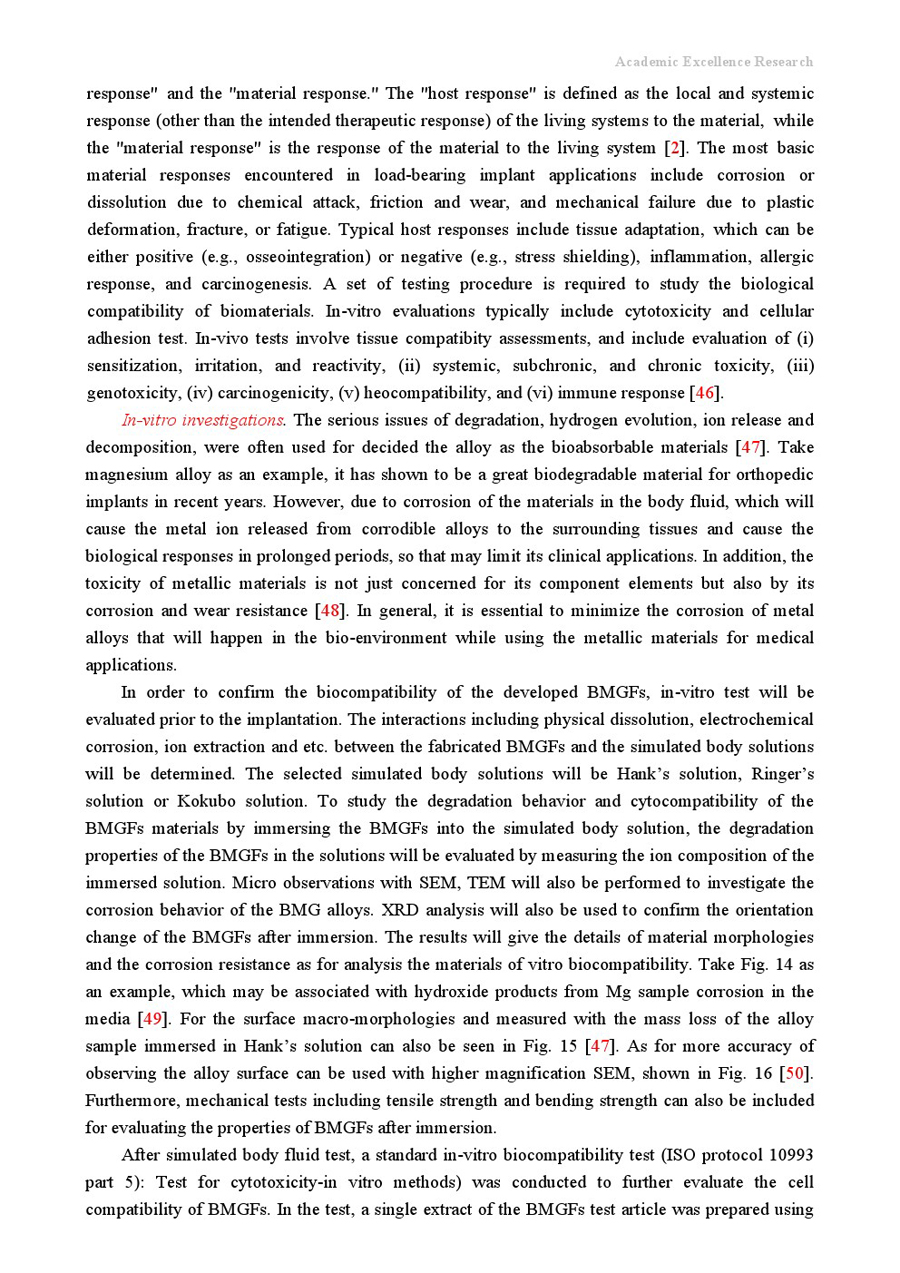 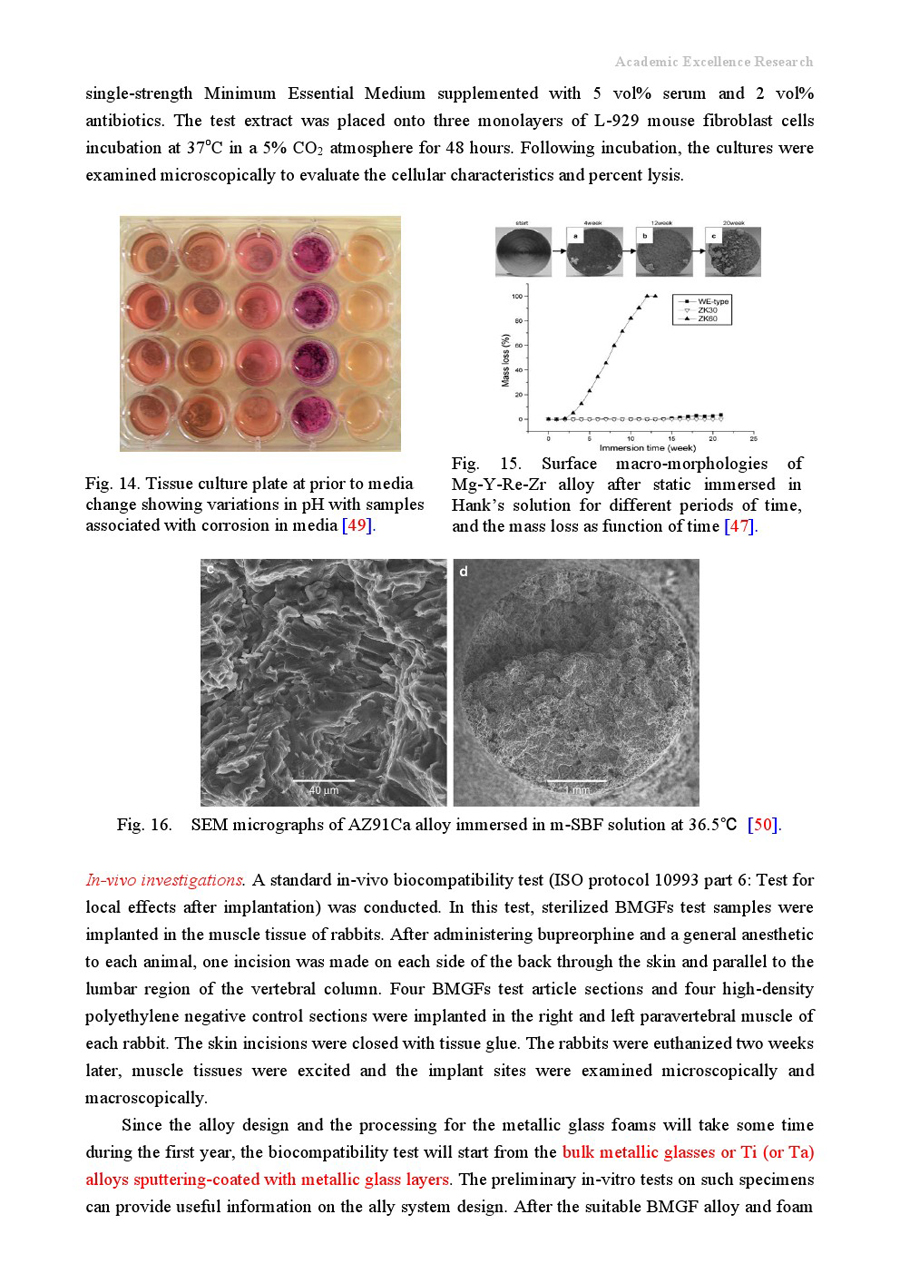
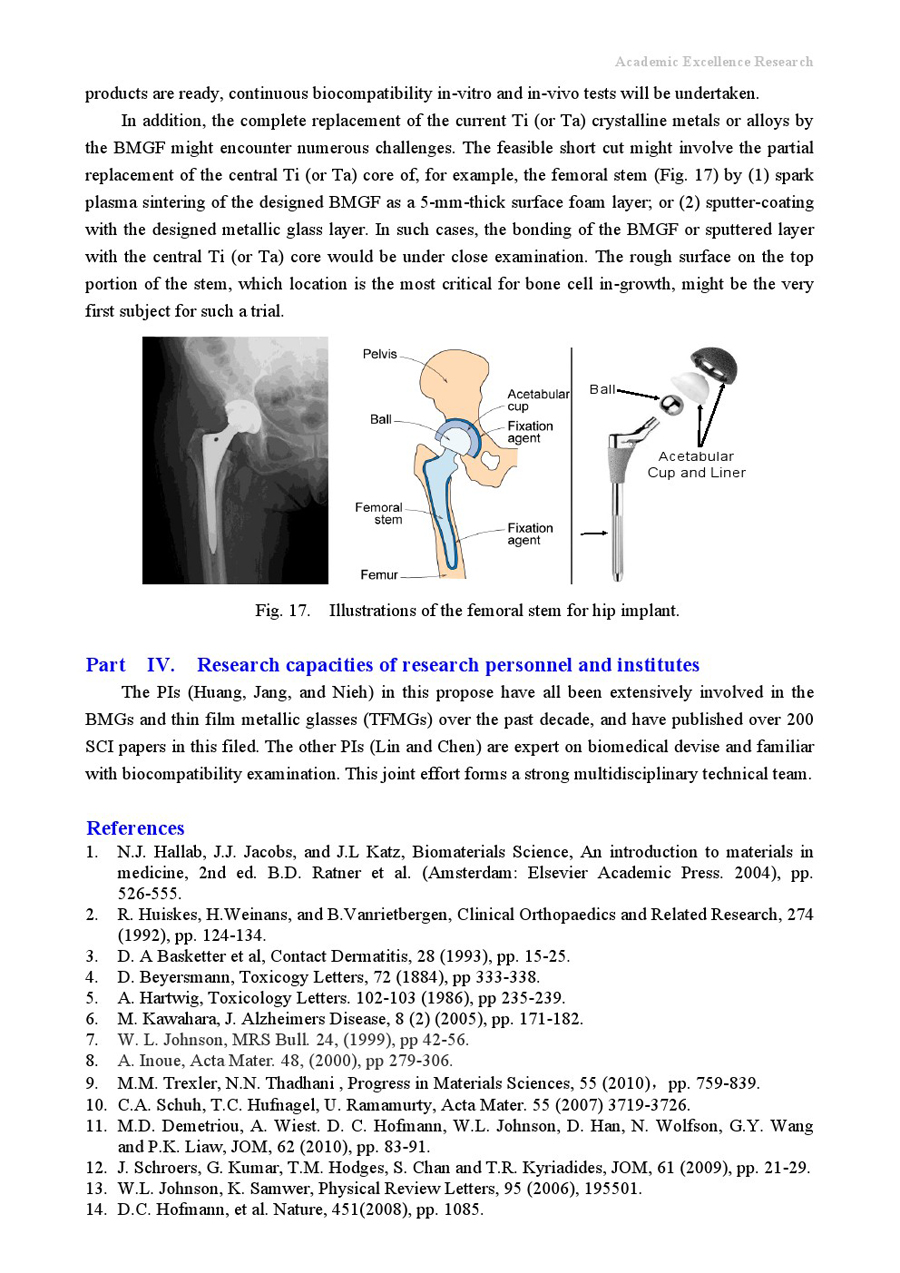 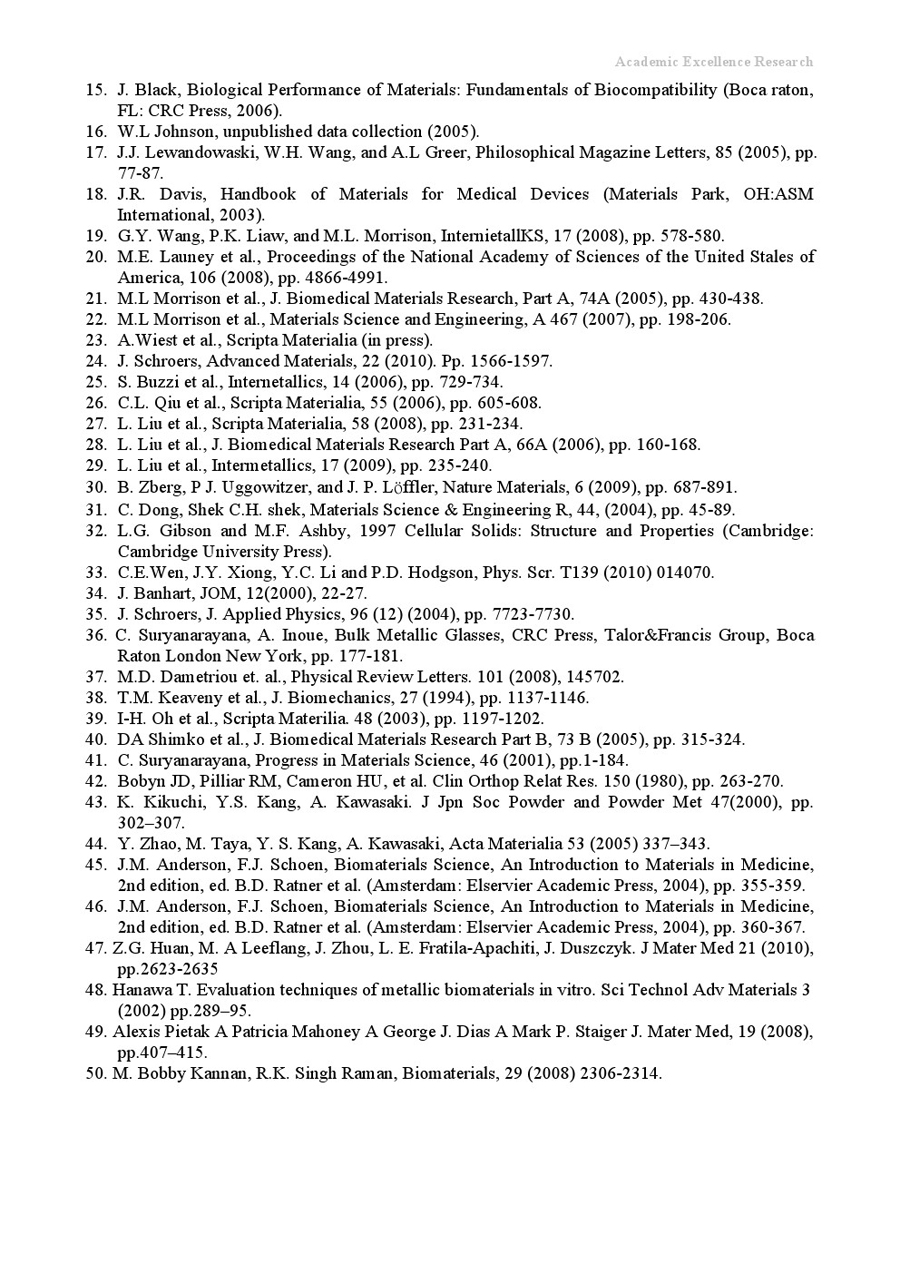
(1) 新近成功研發出在6061鋁合金中添加1%SiO2之納米級粉粒,
於
10-1 - 10o s-1
有
310% 以上之高速超塑性,其成本比6061/15%
SiC(p)
複材低得多。此項成果與鋁材或鎂材在
230oC及102
s-1
之低溫高速超塑性,是近來之重要突破。至於超塑性成形,以自行裝配之成形機、大量氣吹簡單形件、對入模角、潤滑粉及表面層影響等,已有具體結果。
並與機械所黃永茂教授合作,發展電腦模擬與數值分析,
從基本逐步推展,現已對入模角、潤滑作用、材料因子、壓力和成形速率相互轉換等,能模擬與實驗相合之數據。也曾合作對自行開發且呈現低溫超塑性之鎂合金無縫管材,作液壓成型hydroforming。對於金屬複合材料方面,曾檢視長纖與塊狀的複材性質,也從事塊狀鋁基複材之破壞韌性研究,建立擠型熱處理對破壞韌性之影響評估。另也完成對短纖強化鋁合金在中高溫之微組織合機性變化,複材在高速形變時之韌性增加之原委探討,並致力建立一套
constitutivel equations,分析模擬不同應變速率與溫度之各因子相互關係。在日本召開之International
Conference on Innovation in Superplasticity
國際會議中,受邀報告台灣十年來在超塑性之研發與應用後,接著在
Materials Chemistry & Physics 期刊上發表書面
Review 論文,Materials
Chemistry and Physics, vol. 57,國際間突然對國內及華人間之成果,甚表興趣,幾次後續之國際會議皆強力邀請國內之學者出席參加,本人也盡力發函鼓吹,似乎是一種良性的國際交流。後續之發展也很有幸地擴展為海峽三地之整合,建立了一交流管道,收集到從事超塑性之華人學者名單約60人,有國際會議或相關資訊,可以互通消息,也將收集之大陸研發應用,提供給國內如金屬中心參考。在四次國際會議中,也發揮了若干作用,均有海峽三地不少學者參加,相互研討。這種整合意外地帶來日本學界與產業界之高度興趣,如日本超塑協會秘書長
Prof. Kenji Higashi 兩度來台尋求合作,日本
New Energy and Industrial Technology Development
Organization (NEDO) Project Leader Dr. Yukio Ito積極收集台灣相關資料,除學界如中山大學參加合作外,工材所與金屬中心等也極力參與,特別是在鎂合金之超塑性方面。也因此機緣,先後與中鋼公司與金屬中心合辦輕金屬與超塑性應用之產學交流會,推動學術與產業交流互動。這在式微之金屬相關領域,或是應該繼續努力之處。以上並非學術研究成就,僅是近年來努力推動之報告。
(2)
自2001年,逐漸轉鎂基或鋯基奈米或非晶質材料之研發,使用電弧融煉墬落急冷法、旋噴急冷、累積滾壓、噴覆成型法、與高擠型比法等,開發輕量型硬質材料。也開始結合輕量鎂合金與輕量高強度高分子,研製輕量超高比強度複材,已有良好成果。
(3)
近幾年來,因國內開始大量使用鎂合金,但對六方晶系材料成形與機性掌握生疏,故多方探討六方晶系鎂合金之晶粒細化與織構特性,使用XRD/ODF、SEM/EBSD、
TEM/Diff 技術,並發表近十篇相關論文,包括一篇Review論文(Y.
N. Wang and J. C. Huang, “Texture Analysis on Hexagonal Materials”,
Materials Chemistry and Physics, vol. 81, 2003, pp. 11-26)。
(4)
延續材料細化之精神,這兩年與義守與成功大學共同開發鎂基奈米複合材料,有效均勻摻合奈米陶瓷粉於鎂合金或高分子,改善基材性質。
(5)
對非晶質材料之配製與性質分析,乃從2000年開始,現正以
Accumulative roll bonding、drop
casting、melt
spinning三種方式,研製鋯基與鎂基之非晶質或奈米材料,已作出10
mm以上直徑之非晶質棒材,也提出於
2 nm附近之非晶質與奈米晶之臨界相變化理論,並使用分子動力模擬,探討原子混成之正陸續發表於Appl.
Phys Lett., Phys Rev. B, Intermetallics, Scripta Mater, J. Non-Crystalline
Solids, etc。自2005年開始,獲得國科會研究績優團隊國際合作計畫,為期三年,除國內共八位教授參與,另有美國四位院士/會士合作,即Oak
Rideg National Lab 之Dr.
C. T. Liu,Wisconsin
Univ 之Prof.
Y. A. Chang,Univ
of Tennessee 之Prof.
T. G. Nieh與
Prof. P. K. Liaw。
在四年之間,將國內在金屬玻璃之領域,提升至國際知名團隊,成功研發Mg-,
Zr-, Cu-, Al-, A-, Pd-based bulk metallic glasses (BMGs) and thin film
metallic glasses (TFMGs),對製程、微組織、相變化、機性、FIB微奈米尺度性質、微奈米級精密轉印成形等,多次在各大國際會議中,排為首日上午之重要邀請發表者。近五年內之代表作五篇主要在研究金屬玻璃相關理論與實驗,部分成果已經透過金屬中心作媒合,應用於生醫、光電、微機電、表面處理等領域,詳情請參照所附之Review
papers: (1) Intermetallics, vol. 17, 2009, pp. 973-987,(2)
J of Metals, vol. 62, no. 4, 2010, pp. 19-24.
回頁首 |